Mr Clive
|
posted on 21/8/06 at 10:08 PM |
|
|
Tube Joints
When joining two chassis tubes, which would be the best way to do it?
a)
b)
a) is slightly lighter & might mean rust proofing such as waxoyl is easier to apply. a) is also a lot more work than b) but I would like to know
if the loss in strength or stiffness, would be significant?
Thanks 
|
|
|
kb58
|
posted on 21/8/06 at 10:11 PM |
|
|
"B", because it's so much easier to do. I don't know the strength loss of "A".
Virtually no one does "A", though that in itself doesn't mean anything...
[Edited on 8/21/06 by kb58]
Mid-engine Locost - http://www.midlana.com
And the book - http://www.lulu.com/shop/kurt-bilinski/midlana/paperback/product-21330662.html
Kimini - a tube-frame, carbon shell, Honda Prelude VTEC mid-engine Mini: http://www.kimini.com
And its book -
http://www.lulu.com/shop/kurt-bilinski/kimini-how-to-design-and-build-a-mid-engine-sports-car-from-scratch/paperback/product-4858803.html
|
|
indykid
|
posted on 21/8/06 at 11:22 PM |
|
|
if you're bothered about the weight saving of a, i can't think why you'd want to consider rustproofing! heavy stuff for no real
gain.
if the tube's sealed, as in b, it can't rust anyway once the oxygen in the tube's used up.
i'd say b
tom
|
|
Kissy
|
posted on 22/8/06 at 05:36 AM |
|
|
'A' can be useful if you need an exhaust path for welding gases to escape just as you close up a joint. I'd leave enough land
inside the tube for weld penetration, so for example with 25mm(1" o/d tube with 2mm wall I'd drill circa 16mm.
|
|
suparuss
|
posted on 22/8/06 at 05:58 AM |
|
|
knowing how much of a pain it is to drill holes in round tube and considering the insignificant weight advantage of 'A' id use
'B'. it never crossed my mind to drill out the tubes like that when i was building my chassis. there are other much much easier ways to
save weight. like use a hacksaw a files instead of a grinder, by the time youve finished the car youll probably be lighter! 
|
|
locostv8
|
posted on 22/8/06 at 07:42 AM |
|
|
Actually C. I had never thought of that but drilling a hole is much easir than fishmouthing tubing if the hole could be drilled in exactly the right
spot.
http://wrangler.rutgers.edu/gallery2/v/7slotgrille/hssss/
|
|
kb58
|
posted on 22/8/06 at 01:44 PM |
|
|
Huh... you have a verygood point there. If you have do not have a tubing notcher, yes drilling a hole and leaving the tube end square would be faster
than shaping it. OTOH if you have a notcher, no time or effort is saved.
Mid-engine Locost - http://www.midlana.com
And the book - http://www.lulu.com/shop/kurt-bilinski/midlana/paperback/product-21330662.html
Kimini - a tube-frame, carbon shell, Honda Prelude VTEC mid-engine Mini: http://www.kimini.com
And its book -
http://www.lulu.com/shop/kurt-bilinski/kimini-how-to-design-and-build-a-mid-engine-sports-car-from-scratch/paperback/product-4858803.html
|
|
caber
|
posted on 22/8/06 at 01:57 PM |
|
|
If you have a 25mm holesaw and a bench drill with an adjustable table and vice then you have all you need for notching. I would have thought putting a
25mm hole in a 25mm tube would really weaken it even when the other tube was welded in, it might be worth a little experiment though next time I am
notching tube!
Caber
|
|
kb58
|
posted on 22/8/06 at 04:05 PM |
|
|
Yes I'd certainly expect it to be weaker, but by how much I don't know.
Mid-engine Locost - http://www.midlana.com
And the book - http://www.lulu.com/shop/kurt-bilinski/midlana/paperback/product-21330662.html
Kimini - a tube-frame, carbon shell, Honda Prelude VTEC mid-engine Mini: http://www.kimini.com
And its book -
http://www.lulu.com/shop/kurt-bilinski/kimini-how-to-design-and-build-a-mid-engine-sports-car-from-scratch/paperback/product-4858803.html
|
|
DIY Si
|
posted on 22/8/06 at 07:43 PM |
|
|
Err, isn't a 25mm hole in a 25mm tube just notching two tubes at once? Ie twice (possibly) the hassle as just notching the original tube? If
putting a 16mm tube n a 25mm tube, then it'll save much hassle. And once welded it probably isn't much different strength wise.
“Let your plans be dark and as impenetratable as night, and when you move, fall like a thunderbolt.”
Sun Tzu, The Art of War
My new blog: http://spritecave.blogspot.co.uk/
|
|
JoelP
|
posted on 22/8/06 at 08:58 PM |
|
|
id just drill a 4mm or so hole if i was worried about waxoyl, but since im not really id probably not bother at all. 
|
|
locostv8
|
posted on 23/8/06 at 12:28 AM |
|
|
quote: Originally posted by kb58
Huh... you have a verygood point there. If you have do not have a tubing notcher, yes drilling a hole and leaving the tube end square would be faster
than shaping it. OTOH if you have a notcher, no time or effort is saved.
I have neither a notcher nor a drillpress. They are on THE LIST. Something I would like to pass on though. I had to drill some 2" holes thru
the winch mount push bar assy on my Crawler/Jeep/Truck/thingy and nearly took my arm off when the drill bit mounted in the hole saw broke. Not smart
enough to evaluate the cause I replaced the drill bit and broke another within seconds. It is important that the locating piece of the hole saw be
round smooth material, the shank of the drill or as I do now a smooth mandrel, not the flutes of a drill bit. The flutes will catch then bind and
break leaving the hole saw running amuck.
http://wrangler.rutgers.edu/gallery2/v/7slotgrille/hssss/
|
|
Simon S
|
posted on 27/8/06 at 06:17 PM |
|
|
Tube Notching
I used option B, the tube miter Excel programme and 1mm thick cutting discs. Once you got the hang of it I found it could be done quite quickly. I
also tried using tube cutters in a bench drill & it was very messy, providing a much less accurate job than the Miter profiles and a bit of
careful cutting.
Have fun!
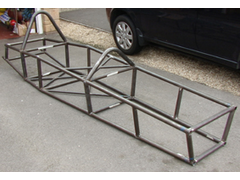 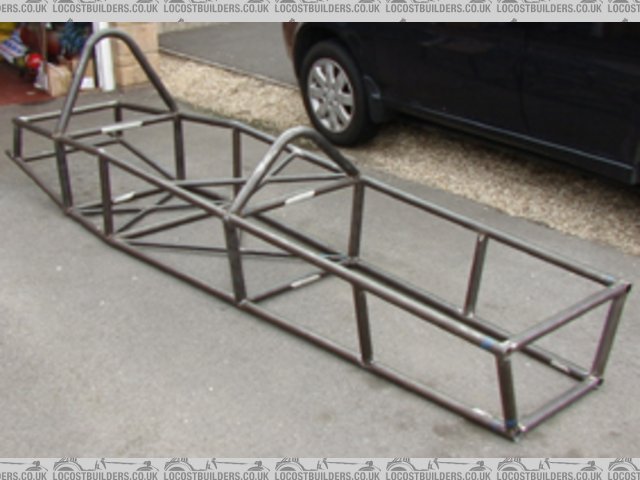 Rescued attachment August 2006 009a.jpg
|
|
dilley
|
posted on 27/8/06 at 06:27 PM |
|
|
Ive heard glueing is good 
|
|
coozer
|
posted on 28/8/06 at 06:44 PM |
|
|
quote: Originally posted by dilley
Ive heard glueing is good
only for your hand to your face...  
1972 V8 Jago
1980 Z750
|
|