mistergrumpy
|
posted on 13/10/08 at 12:17 PM |
|
|
Metal Working
Saw an awesome build a while back of a 32 Ford Model A pick up truck and one thing that always got me thinking was the shape of the roof.
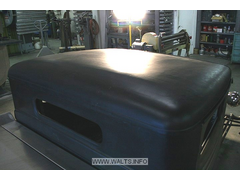 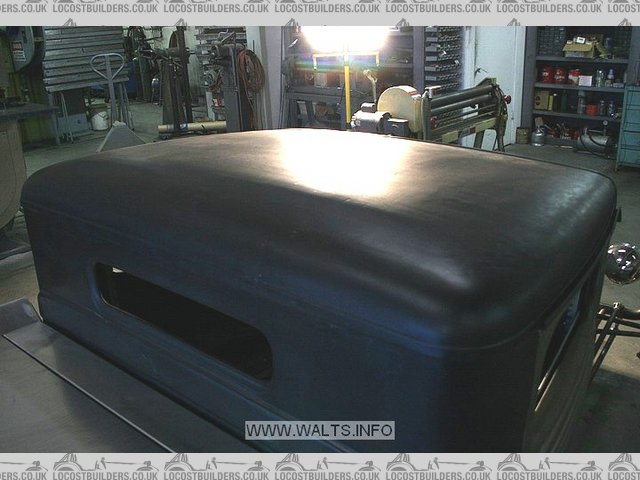 Model A Roof
How would this be originally made? It is a single panel but would it have been welded out of sections, stamped or wheeled and what kind of thickness
of steel would it be as it has no supporting frame and would have to hold its own weight.
It got me thinking as I used to do leadworking in a past life and I reckon I could make one out of lead but it would be fairly big job.
|
|
|
JeffHs
|
posted on 13/10/08 at 12:52 PM |
|
|
Did you ever see Clarkson in Cuba? There was a piece on there where 2 guys made a brown paper template of the front wing of a Cadillac, then proceeded
to bash a sheet of steel with hammers until they'd got the right shape.
I have done a lot of very amateurish panel beating. I am in awe of the experts.
|
|
mistergrumpy
|
posted on 13/10/08 at 12:58 PM |
|
|
No I didn't see that one. I used to use the same technique with lead. Dressing it into obscure shapes and just moving the thickness of the metal
around really but to do it on steel, surely you'd need arms like Popeye's?
|
|
JAG
|
posted on 13/10/08 at 01:19 PM |
|
|
If made today they would use several large presses and a 'progression tool'.
The tool would have several impressions; the first would be a rough shape similar to the final shape and the final one would be the shape you wanted.
In between there would be other impressions each one would be a step closer to the final shape. The number of impressions depends upon the complexity
of the shape you're making.
The blank sheet would start in the first impression and be moved along after each blow until it reached the last impression where it would pop out
looking like your panel but with some flash around the outside. The flash would then be trimmed of in another special tool.
I don't know when this technology was first used so that roof panel may have been made by this method or it may have been more hand made.
However Henry Ford was one of the first to use mass-production methods so it may well have been a progression tool.
Justin
Who is this super hero? Sarge? ...No.
Rosemary, the telephone operator? ...No.
Penry, the mild-mannered janitor? ...Could be!
|
|
Mr Whippy
|
posted on 13/10/08 at 01:49 PM |
|
|
quote: Originally posted by mistergrumpy
I reckon I could make one out of lead but it would be fairly big job.
you trying to compete with speedyxjs for - who can make the heaviest car?
[Edited on 13/10/08 by Mr Whippy]
Fame is when your old car is plastered all over the internet
|
|
MikeCapon
|
posted on 13/10/08 at 02:35 PM |
|
|
At the time I reckon it would be several panels welded together and then lead loaded to the final shape.
A very very long time ago I worked on the Rolls Silver Spirit body line. The joint along the top of the front wings was made using spot welds in a
recess which was subsequently filled with lead. Same thing with the classic Rolls shaping around the headlight area. All lead.
At the time there was over 80 kilos of lead in a Silver Spirit body. More than a decent engine weighs
Still it wasn't at all dangerous... Oh no, not at all. All the guys working with the lead were given a free bottle of milk a day to drink and
that was supposed to stop them from getting poisoned
So that was alright then.......
|
|
owelly
|
posted on 13/10/08 at 05:11 PM |
|
|
I saw a guy craft the front panel for a VW Camper van out one sheet of steel. It took two days of tapping with varuious bits of wood, dollies, sand
bags, hammers and a few bottles of whiskey.
http://www.ppcmag.co.uk
|
|
mistergrumpy
|
posted on 13/10/08 at 05:13 PM |
|
|
Ah. I'd never heard of progression pressing. I too thought about lead loading and a single press but didn't think either were practical.
Slow processes and heavy in the case of the lead.
I think that pressing must have been used due to the trim around the window bottoms. Its like a double bump.
What kind of thickness steel would have been used? Most likely thicker than todays standards as they seem to have a skeletal frame underneath now.
|
|
COREdevelopments
|
posted on 13/10/08 at 05:21 PM |
|
|
have you ever seen american hotrod series? if not you really need to see the first series with the ALU TUB car, they make the whole body from ali!
really interesting to watch.
rob
|
|
mistergrumpy
|
posted on 13/10/08 at 05:28 PM |
|
|
American Hotrod? Never heard of it. Is that its actual name? It sounds like some kind of american chopper spin off?
I'll have to look for DVD's of it.
|
|
Litemoth
|
posted on 13/10/08 at 07:34 PM |
|
|
I'm pretty sure it would have been 'stamped' in a press brake. All of the radii are nice and big so 'deep draw' would be
my bet.
Henry Ford was banging out a Model T every 90 mins in 1913 and you can bet he wasn't hand crafting a single panel by welding 17 or so bits
together.
The cab has quite a few sophisticated profiled and curved panels - no way they'd have hand made 'em and stayed in business.
|
|