trogdor
|
posted on 18/1/07 at 02:53 PM |
|
|
sure we have one of those in the aladdins cave! my dads garage is so small u can't get a car in but it has so many tools!
so if the casing is 10mm thick, how far should i go? about 80% of the casing ie 8mm?
|
|
|
macnab
|
posted on 18/1/07 at 02:53 PM |
|
|
top tap would be used to finish off the hole once the tapered ones have been used, so that you have the maximum thread depth.
Yeah 8mm would be fine...
[Edited on 18/1/07 by macnab]
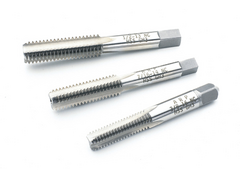  Rescued attachment new_products_arp_01.jpg
|
|
trogdor
|
posted on 18/1/07 at 03:06 PM |
|
|
coolio, now i need to get one of these cylinders and a suitable spacer made! what materials are the best to use
i assume a chunk of ally would be best?
where can get some? is it expensive?
at least my car is already set up for hydralic clutch!
[Edited on 18/1/07 by trogdor]
|
|
macnab
|
posted on 18/1/07 at 03:16 PM |
|
|
allys not expensive!
Got to a scrap metal merchant and find a small block, tenner at most
|
|
trogdor
|
posted on 18/1/07 at 03:24 PM |
|
|
shows how much i know!
cool will have to sort some out, the main prob is going to be the machining and measuring but i can prob find a machinst in runcorn there is alot of
that sort of industry around here.
is the saab 900 release bearing ok with a zetec clutch or does it have to be another one? ie is it rounded, its not obvious from the pics that i have
found.
|
|
tks
|
posted on 18/1/07 at 03:57 PM |
|
|
mhhh
You could also maybe use some other holes / bolts
for example the ones where the box join the belhousing.
If you could get 3/4/5mm sheet.
You would just cut a "gasket" wich in the middle has the hole for the gearbox input shaft.
then around that hole you could drill and shampfer the holes, weld in a shampfer bolt and to that bolt you could easyly mount your spacer. In that way
you don´t need to play with the casting.
Thinking about the forces in fact the onlyy thing it should be able to survivie is the bearing resistance at max rpm.
sow any piece of sheet could do it.
or just some straps.
wy not use a normal slave cilinder wich is outside the belhousing?
With a bit of angle it should be able to build a mount and tab / screw that to the housing!! the big advantage is there that
if your clutch needs some adjustment..
you then just could make sleeves instead of holes in your support.
hope you get it and it makes sense...
also make sure while measuring the slave cilinder is fully in!!
TKs
[Edited on 18/1/07 by tks]
The above comments are always meant to be from the above persons perspective.
|
|
Schrodinger
|
posted on 18/1/07 at 04:09 PM |
|
|
Looking at your first posting it doesn't look as though the bell housing is very deep. Try putting a straight edge across the BH and measure the
distance to the release bearing and compare this to a type 9. You might also want to measure the distance from the flywheel mounting face on the Zetec
to the gearbox flange again compare this to the Saab engine.
The combination of these measurements should give you some idea of the size spacer you will need.
You could also try using a CRB from a 1971-88 Ford Transit 2.4/2.5 diesel (Quinton Hazell part CCT303) which is a deeper bearing and is used with a
T9/Zetec combo to reduce the throw.
|
|
NS Dev
|
posted on 18/1/07 at 04:16 PM |
|
|
Saab 900 bearing is indeed round nose you will be pleased to hear!!!
£15 from your local stockist, slave cyl around £40
To work out the measurements, use the AP sheet to get the compressed depth of the cylinder from rear mounting face to front face of bearing, then add
4-5mm for some free play to allow for clutch wear.
Next measure your clutch and flywheel in situ on the engine. you need the fitted height from the tips of the clutch fingers to the back of the engine
block face, easiest is to put a straight edge across the clutch fingers to extend across to just outside the flywheel, then measure with a ruler from
the block face to the inside of the straight edge.
Add up the slave and bearing height, the free play 5mm plus the depth you just measured, and compare it to the measurement from front of bellhousing
to the face you plan to mount the cylinder on at the back of the bellhousing.
The amount that the bellhousing is greater by is the thickness of spacer needed.
Retro RWD is the way forward...........automotive fabrication, car restoration, sheetmetal work, engine conversion
retro car restoration and tuning
|
|
NS Dev
|
posted on 18/1/07 at 04:19 PM |
|
|
ps the face of that alloy block in the piccy is not flat, front or back!
The back is machined out to allow the oil seal in there and the front is recessed behind the slave as it sits in a small recess. This machined recess
also keeps it dead concentric, the bolts just pull it into the recess firmly, they don't locate it on the face at all.
Retro RWD is the way forward...........automotive fabrication, car restoration, sheetmetal work, engine conversion
retro car restoration and tuning
|
|
NS Dev
|
posted on 18/1/07 at 04:20 PM |
|
|
ps ps I'll see if I drew it, I usually do before I set to on the lathe
Retro RWD is the way forward...........automotive fabrication, car restoration, sheetmetal work, engine conversion
retro car restoration and tuning
|
|
tks
|
posted on 18/1/07 at 04:22 PM |
|
|
mhh
would just make it external allot easier faster and more fool proof.
only thing is you need the space..
Tks
The above comments are always meant to be from the above persons perspective.
|
|
trogdor
|
posted on 19/1/07 at 09:03 AM |
|
|
i already have an external slave cylinder, but my problem is having a clutch release bearing that is flat faced when i need it to be rounded
i am thinking the best bet is with the saab 900 slave as i can't see any obvious way of making the crb rounded, if anyone knows of a crb that is
rounded that will fit that would be great but i have doubts about that since this gearbox was designed by saab and only used by them.
unfortunatly i can't use the bolts where the bellhousing joins the gearbox as there aren't any.the gearbox and bell housing are in one
piece but that would of been a good way around it
damn this is harder than i hoped it would be, am asking on another forum for the casing thickness at the front of the gearbox, no answer yet tho
[Edited on 19/1/07 by trogdor]
|
|
trogdor
|
posted on 19/1/07 at 12:31 PM |
|
|
oooh a diagram of your spacer would be great ns dev, would like ot know general diemensions and how the front needs to be machined, will have to
measure the lumps and bumps on my gearbox so i can get the back of my spacer ready!
|
|