MautoK
|
posted on 12/6/09 at 04:35 PM |
|
|
Spigot bearing removal (Done!)
L&G,
I have a 'new-to-me' Pinto 2L replacement and am converting it from manual to automatic. Clutch & flywheel are off and I now need to
remove the spigot bearing. The torque converter has a 3/4" dia spigot that engages in the spigot bearing hole.
I have a piece of wood dowel that's a nice snug fit in the ID and have tried packing it with grease to hydraulic it out, but it's not
budging.
Do I persevere or take the destructive approach and lever it out?
Thanks,
John.
[Edited on 14/6/09 by MautoK]
He's whittling on a piece of wood. I got a feeling that when he stops whittling, something's gonna happen. (OUATITW/Cheyenne)
|
|
|
tomprescott
|
posted on 12/6/09 at 04:43 PM |
|
|
Use a universal fitting tool (hammer!) in conjunction with a drift to apply some power to your lever - but be careful.
|
|
MautoK
|
posted on 12/6/09 at 04:52 PM |
|
|
Tom,
Yes, I'm whacking the dowel with a hammer but the bearing is not interested...!
John.
quote: Originally posted by tomprescott
Use a universal fitting tool (hammer!) in conjunction with a drift to apply some power to your lever - but be careful.
He's whittling on a piece of wood. I got a feeling that when he stops whittling, something's gonna happen. (OUATITW/Cheyenne)
|
|
Land Locked
|
posted on 12/6/09 at 05:02 PM |
|
|
Try window putty instead of grease, it's thicker and tends to stay put better.
|
|
MautoK
|
posted on 12/6/09 at 05:04 PM |
|
|
Good thinking, that man!
I'll try that (if my pot of putty is still workable...)
quote: Originally posted by Land Locked
Try window putty instead of grease, it's thicker and tends to stay put better.
He's whittling on a piece of wood. I got a feeling that when he stops whittling, something's gonna happen. (OUATITW/Cheyenne)
|
|
MautoK
|
posted on 12/6/09 at 06:15 PM |
|
|
Conspiracy of tolerances is at work!
It's become an un-reuseable bearing now; the needles are out and I tried to collapse the outer race but it won't play.
I don't have a grinder small enough to get in there, so going to try making a puller with two six inch nails, flats filed on each head so
they'll lock in behind the inner rim. Then either a long bar welded to the nails' pointy ends to make a slide hammer or a lever
arrangement might do it.... We'll see!
Any other ideas?
He's whittling on a piece of wood. I got a feeling that when he stops whittling, something's gonna happen. (OUATITW/Cheyenne)
|
|
lotusmadandy
|
posted on 12/6/09 at 07:05 PM |
|
|
I used a dremmel with a small grind stone
to grind through a narrow section of the side wall.It worked a treat.
Andy
|
|
Danozeman
|
posted on 12/6/09 at 08:28 PM |
|
|
Slide hammer!!!
Dan
Built the purple peril!! Let the modifications begin!!
http://www.eastangliankitcars.co.uk
|
|
jollygreengiant
|
posted on 12/6/09 at 08:40 PM |
|
|
Use a suitably sized Rawl bolt in the hole with a LARGE thick washer. When thew rawl bolt is tightened you can then lever against the washer and hey
presto out it pops as easy as pie.
Total cost of this low cost tool - about £3 tops.
Beware of the Goldfish in the tulip mines. The ONLY defence against them is smoking peanut butter sandwiches.
|
|
flak monkey
|
posted on 12/6/09 at 08:50 PM |
|
|
The other option is a small cold chisel to break the outer race.
All the ones I have done have come out either with grease or a bolt hooked on the inside and used like a slide hammer.
David
Sera
http://www.motosera.com
|
|
Land Locked
|
posted on 12/6/09 at 09:01 PM |
|
|
quote: Originally posted by flak monkey
The other option is a small cold chisel to break the outer race.
When all else fails, the tiny cold chisel bought for this job.
|
|
02GF74
|
posted on 12/6/09 at 09:01 PM |
|
|
hahaha I replaced one of these this week, crossflow but same principle.
I tried the drift technique - fitted an aluminium tube onto a drift so it is a snug fit, filled up with grease and introduce mr hammer.
no budging, could I get the drift out? could I f***. there I was, with probably was was a good bearing not knacked with a hardened steel drift
poking out the end.
let's say I was not a happy buuny.
fortunatley with some side to sdie movent got the drift out and this time introduce mr dremel with small grinding disc.
about 5 - 10 mins managed to grind through the race enough to collapse it and using a samll chisel, poke it out.
trhing to crack the race with a chisel resulted in denting the chisel - grind it out is my recommendation.
I didthink of getting a rawl bolt - you know the expanding cone type and then rigging up something that I could hammer but didn't - that may
have worked. (that method was successful in removing the piston from a sierra master).
|
|
flak monkey
|
posted on 12/6/09 at 09:05 PM |
|
|
quote: Originally posted by 02GF74
trhing to crack the race with a chisel resulted in denting the chisel - grind it out is my recommendation.
Your chisel obviously wasnt man enough for the job then
A well placed clout with a small cold chisel will invariably crack the race with all but minor damage to the chisel. (Obviously some damage will occur
as a bearing race is ~60Rc)
David
Sera
http://www.motosera.com
|
|
mark chandler
|
posted on 12/6/09 at 09:18 PM |
|
|
Bit of weld on the inside of the bearing race will cause it to distort and shrink, should just drop out then.
|
|
ss1turbo
|
posted on 12/6/09 at 10:15 PM |
|
|
I do tend to get rather "medieval" on these things - never had one pop out by the grease method yet; always had to resort to a good
chisel.
I have many success stories with the rawl bolt/slide hammer trick, but needs a big slide hammer to work..
Long live RWD...
|
|
bimbleuk
|
posted on 13/6/09 at 06:39 AM |
|
|
quote: Originally posted by jollygreengiant
Use a suitably sized Rawl bolt in the hole with a LARGE thick washer. When thew rawl bolt is tightened you can then lever against the washer and hey
presto out it pops as easy as pie.
Total cost of this low cost tool - about £3 tops.
I did it this way on my 4AGE much cleaner than the grease method! I bought some threaded rod a rawl bolt a couple of nuts and washers. At the other
end I had a lump of metal I could slide up and down the threaded rod to make a slide hammer.
[Edited on 13-6-09 by bimbleuk]
|
|
02GF74
|
posted on 14/6/09 at 12:19 PM |
|
|
quote: Originally posted by flak monkey
quote: Originally posted by 02GF74
trhing to crack the race with a chisel resulted in denting the chisel - grind it out is my recommendation.
Your chisel obviously wasnt man enough for the job then
I don't deny it - it is a tiny chisel, maybe the thickness of a pencil that I manageto bend!!!
Here is a removed spigot bearing last week.
 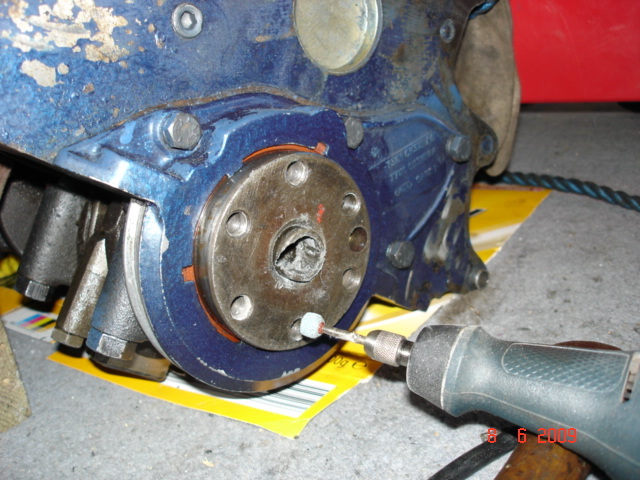 Rescued attachment DSC04694.JPG
|
|
MautoK
|
posted on 14/6/09 at 09:42 PM |
|
|
Well it's out!
Bought a Dremel this morning; a rather non-locost solution, but at least I've retained my sanity.
I've swapped all the external bits to the 'new-to-me' engine and adjusted the valve clearances.
The great spline god was not in a friendly mood and it took 30 minutes to get the auto box attached. Is it just me, or do you find that either it goes
straight on first try or it takes about 100 attempts?
So now the (replacement) engine and (recent replacement) autobox are back in the car.
Tomorrow, connect everything back together, make sure there's oil pressure, do a compression test for reference then turn the key...
John.
He's whittling on a piece of wood. I got a feeling that when he stops whittling, something's gonna happen. (OUATITW/Cheyenne)
|
|