sdh2903
|
posted on 27/8/15 at 05:44 PM |
|
|
Sheared bolt
Well after a productive day on refurbing my donor engine I dropped a bollock and sheared a bolt on the oil pick up. I know I'm a tit. Now
what's the consensus on rectification?
 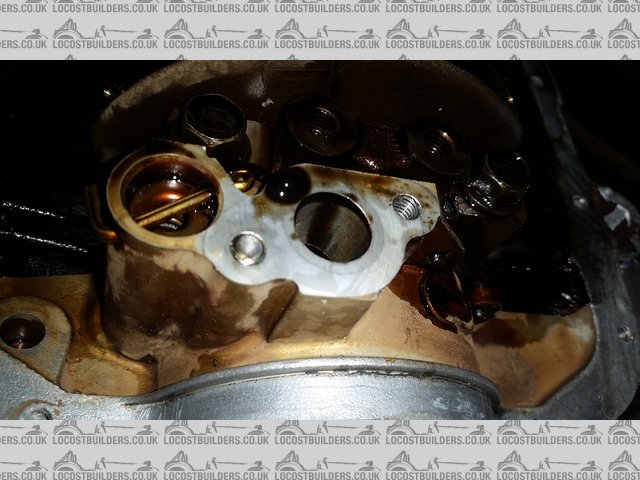 Sheared
It's an m6 fine bolt. I can either
A. Drill and easy out. I have decent snap on ones but still risky.
B. Drill out the bolt close to diameter and re tap. New fine tap and bolt required.
C. Drill out and helicoil and stick a normal pitch m6 bolt in.
Best solution? I'm edging towards C as I already have all the necessary tools to do it.
[Edited on 27/8/15 by sdh2903]
[Edited on 27/8/15 by sdh2903]
|
|
|
theprisioner
|
posted on 27/8/15 at 05:59 PM |
|
|
Stuff cloths in the obvious places and cut a screwdriver slot in the bolt remains and see if it moves. Failing that make an ally plate screen just
letting the remains of the bolt show thru then weld a leaver on to it. The welding heat loosens the bolt. The leaver does the rest.
http://sylvabuild.blogspot.com/
http://austin7special.blogspot.co.uk/
|
|
adithorp
|
posted on 27/8/15 at 06:02 PM |
|
|
Bolt or stud? Stud would generally be tighter were a bolt, once the heads gone might not be.
Is it stood slightly proud? If so I'd try using a dremel to cut a screw driver slot in it.
Not a fan of easy-out, especially small ones. They either snap (a d then your FUBAH) or expand the bolt making it tighter. I've had successful
drilling then knoki g a TORQ bit in.
"A witty saying proves nothing" Voltaire
http://jpsc.org.uk/forum/
|
|
Paul Turner
|
posted on 27/8/15 at 06:23 PM |
|
|
Simple solution, new oil pump. No risk of damaging any other components or getting swarf into the oil galleries.
Do it right, do it once.
|
|
sdh2903
|
posted on 27/8/15 at 06:38 PM |
|
|
It's a bolt, sheared just below flush. It was winding in fine by fingers then went very tight as i ratcheted it down and as I backed it out it
just sheared. So I don't think the slot/screwdriver method will work.
|
|
mark chandler
|
posted on 27/8/15 at 06:41 PM |
|
|
It looks like it's standing proud so my first choice would be carefully cut a slot and see if you an undo with a screwdriver.
Next try gently trying to knock it around with a sharp punch
Third, drop a nut over it and weld to create a new bolt head
If all that fails drill it out
Regards Mark
|
|
rusty nuts
|
posted on 27/8/15 at 07:04 PM |
|
|
Get the MIG welder out and weld a nut to the end of the bolt , the heat will help and if the weld breaks the weld on another. If that doesn't
move it then your down to drilling and tapping . Welding a nut works on seized bleed nipples, wheel nuts and brake calliper pipe unions amongst others
|
|
SCAR
|
posted on 27/8/15 at 07:30 PM |
|
|
As above. Put a nut over the remains of the bolt and fill the nut centre with weld. The heat will help free the threads. Works 90% of the time
|
|
sdh2903
|
posted on 27/8/15 at 07:35 PM |
|
|
Cheers gents. I will take another Look tomorrow to see if the weld on a nut technique but I suspect it may just be slightly recessed
|
|
SCAR
|
posted on 27/8/15 at 07:49 PM |
|
|
Doesn't matter, you can build the weld up on top of the stud until it starts filling in the centre of the nut.
|
|
MikeRJ
|
posted on 27/8/15 at 09:52 PM |
|
|
If you sheared it due to simply over-torquing rather than damaged/crossed threads making the bolt very tight, then this is exactly the situation that
a bolt extractor should work with negligible risk as you shouldn't need much torque to get it out.
|
|
coozer
|
posted on 27/8/15 at 10:28 PM |
|
|
I snapped off one of the exhaust studs on my rv8.. Managed to drill it out and remove the last few bits of thread.
Ran a tap down to clean it the bugger snapped off!
To get that out I used a carbide bit and hammered away at it to smash it to bits... Managed to get it all out and the thread survived!!
I would try a small drill and an easy out first with lots of penetrating oil...
Good luck!
1972 V8 Jago
1980 Z750
|
|
Shooter63
|
posted on 28/8/15 at 05:40 AM |
|
|
If you can centre punch the remainder accurately use a m5 l/h drill bit, if not a m4.5 to give you a bit of tolerance, plenty of easing fluid and it
should just come out as you are drilling, remember to run the drill backwards obviously.
Shooter
|
|
britishtrident
|
posted on 28/8/15 at 07:24 AM |
|
|
Using easyouts is usually doomed to failure but damage screw extractor bits usually work.
I got a set from Lidl years back and they have worked every time. Silverline market a set as Silverline 675174
Link to item on Silverline
Website
It will help to warn the cast before starting as the light alloy will expand more than the steel
[I] “ What use our work, Bennet, if we cannot care for those we love? .”
― From BBC TV/Amazon's Ripper Street.
[/I]
|
|
motorcycle_mayhem
|
posted on 28/8/15 at 09:25 AM |
|
|
I'd go for the EZ-Out.
Without seeing it, this appears to be a non-corroded, non-abused fitting that has simply sheared. I suspect it's therefore fairly labile.
OK, so if it's cross-threaded, abused, threadlocked or is buried in corrosion I'd hit the welding torch.
|
|
loggyboy
|
posted on 28/8/15 at 09:50 AM |
|
|
quote: Originally posted by sdh2903
A. Drill and easy out. I have decent snap on ones but still risky.
Whats the risk?
Mistral Motorsport
|
|
britishtrident
|
posted on 28/8/15 at 10:35 AM |
|
|
quote: Originally posted by adithorp
Bolt or stud? Stud would generally be tighter were a bolt, once the heads gone might not be.
Is it stood slightly proud? If so I'd try using a dremel to cut a screw driver slot in it.
Not a fan of easy-out, especially small ones. They either snap (a d then your FUBAH) or expand the bolt making it tighter. I've had successful
drilling then knoki g a TORQ bit in.
+1
[I] “ What use our work, Bennet, if we cannot care for those we love? .”
― From BBC TV/Amazon's Ripper Street.
[/I]
|
|
adithorp
|
posted on 28/8/15 at 11:19 AM |
|
|
quote: Originally posted by loggyboy
quote: Originally posted by sdh2903
A. Drill and easy out. I have decent snap on ones but still risky.
Whats the risk?
That it might (especially being small) break, then you have a hardened broken bit in it that you can't drill.
"A witty saying proves nothing" Voltaire
http://jpsc.org.uk/forum/
|
|
sdh2903
|
posted on 28/8/15 at 02:39 PM |
|
|
First prize and a coconut goes to Adi!
Bolt is out. Tried welding a nut but it just kept shearing off. Went for the drill and knocking a torq bit in and it came out a treat. And a bonus was
it was just a standard m6 thread on closer inspection. Quick clean out with a tap and both bolts replaced. Can now get on with getting the sump back
on.
Cheers guys!
|
|
MikeRJ
|
posted on 28/8/15 at 05:38 PM |
|
|
quote: Originally posted by britishtrident
Using easyouts is usually doomed to failure but damage screw extractor bits usually work.
I agree that Easyouts are doomed to failure when the part that needs to be extracted is seized in place, e.g. through corrosion or cross threading and
I've often advised against their use on here in such situations. However when a fastener has been sheared off like this the threaded part is
rarely very tight, you just need something to be able to turn it with. I've never had an easyout fail in this situation.
A left hand drill bit is sometimes enough to back them out.
|
|