ned
|
posted on 4/4/05 at 03:44 PM |
|
|
exhaust system modelling
no, i don't mean a big bore advert in max power!
Thinking about my exhaust and where to get it made, but am thinking of making something up to give me an idea of the shape/layout/distances i want for
my 4-2-1 system. Maybe something i could give to someone to copy in stainless to save me having to ferry the car to someone to make it.
I'm thinking about nice sand bent tubes so there's no distortion and getting long flowing curves to get good flow. what material could i
use to do this with as a mock-up?
I though about some old steel exhausts chopped about and tacked together, but i doubt i'd get the curves i want from cutting up old road
systems. also the tube diameter would be a bit small.
or is this just a stupid idea?
Ned.
beware, I've got yellow skin
|
|
|
nick205
|
posted on 4/4/05 at 04:03 PM |
|
|
Hi Ned,
What about some foam pipe lagging a la B&Q, with a bit of welding rod/wire stuck to the inside. That should give you roughly the dia. and the
wire will let you bend it around til your hearts content.
Nick
|
|
bigandy
|
posted on 4/4/05 at 06:12 PM |
|
|
That is a genius idea!
Dammit! Too many decisions....
|
|
ned
|
posted on 4/4/05 at 08:06 PM |
|
|
coat hangers and pipe lagging - brilliant - thanks nick!
Ned.
beware, I've got yellow skin
|
|
907
|
posted on 4/4/05 at 10:36 PM |
|
|
Hi Ned,
Just a point to bare in mind before you go wrecking every coat hanger in the house.
The radius of the former the tube is bent round will be fixed. The same applys to dairy bends.
Before you start, find someone that will do the work, then find out what rads they can bend.
It could save doing the mock ups twice.
HTH
Paul G
|
|
NS Dev
|
posted on 5/4/05 at 07:09 AM |
|
|
A very good point 907!!!
What's you opinion (as you're the expert in this area) on building a decent exhaust manifold using hygienic stainless tubing?
I am worried about the number of welds, as there will be a lot of bends to get the lengths right etc. (I have free access to a mate's tig, but
don't want to take the p155!!)
The other problem for me is the lack of 1 3/4" (45mm ish) tube/bends on the market, as I need this size for my primary pipes.
It's just that it would appear to be cheaper the buy 12 or 16 90 degree dairy bends (to get all the angles needed by cutting) and some straight
tube, than to get somebody to form all the pipes.
[Edited on 5/4/05 by NS Dev]
|
|
Jeffers_S13
|
posted on 5/4/05 at 07:17 AM |
|
|
quote: Originally posted by NS Dev
The other problem for me is the lack of 1 3/4" (45mm ish) tube/bends on the market, as I need this size for my primary pipes.
[Edited on 5/4/05 by NS Dev]
http://www.milneroffroad.com/PIPE.HTM
|
|
NS Dev
|
posted on 5/4/05 at 07:22 AM |
|
|
Yes I know about Milner, but they don't do 1 3/4" bends!!
these are a fair bit cheaper as well - cheap stainless steel pipework
|
|
v8kid
|
posted on 5/4/05 at 07:41 AM |
|
|
NS - those bends are seriously heavy nearly 3mm thick walls!! Conventional exhaust tubing is much thinner about 1mm if I remember right and the bends
have a much larger radius.
I used Custom Chrome for my manifold bends and they were very fair to me - sometimes we just have to pay the price.
Stainless aint all its "cracked" up to be. I've had both and with the limited use our type of cars get mild steel lasts ok is
cheaper and easier to weld as you don't have to back purge the pipes.
Cheers
David
|
|
Jeffers_S13
|
posted on 5/4/05 at 07:52 AM |
|
|
quote: Originally posted by NS Dev
Yes I know about Milner, but they don't do 1 3/4" bends!!
Oh yeah ! doh ! sorry !
|
|
Jeffers_S13
|
posted on 5/4/05 at 07:57 AM |
|
|
http://www.cobraclub.com/forum/showthread.php?p=89660#post89660
This thread mentions a place called ABC Metal Services in Stoke on Trent, these Cobra builders are/were having the same problem as you it seems.
|
|
NS Dev
|
posted on 5/4/05 at 11:44 AM |
|
|
quote: Originally posted by v8kid
NS - those bends are seriously heavy nearly 3mm thick walls!! Conventional exhaust tubing is much thinner about 1mm if I remember right and the bends
have a much larger radius.
I used Custom Chrome for my manifold bends and they were very fair to me - sometimes we just have to pay the price.
Stainless aint all its "cracked" up to be. I've had both and with the limited use our type of cars get mild steel lasts ok is
cheaper and easier to weld as you don't have to back purge the pipes.
Cheers
David
The dairy bends are not that thick, all the ones I have had from all stainless ltd have been 16 swg, so 1.6mm wall.
I may yet use custom chrome, they are just down the road from me but I don't like being ripped off, that's the problem!
I am also considering mild steel, for the reasons you mention, but based on quoted so far, I can get the 16swg hygienic 316 stainless bends cheaper
than custom chrome will do mild steel!!!!!!!!!!!!!!!!!!!!!
e.g. allstainlessltd do a 2" 90 deg 316 polished stainless bend for £5.50, 1.5" is £3.78. That is pretty cheap in my book, as I say,
custom chrome wanted more than that for mild steel bends!
|
|
v8kid
|
posted on 5/4/05 at 12:02 PM |
|
|
NS, that is cheap!! I'll have to look properly at that site - thanks for the tip perhaps a swift change of mind is in order
|
|
SteveH
|
posted on 5/4/05 at 12:24 PM |
|
|
Just a couple of Ideas...
Domestic plastic waste pipe can be bent with a heat gun, can be glued & comes in sutible sizes for exhaust mock-up.
Some one on here used it to make a rolebar patern...can't remember who?
MK Engineering do pipe bending, & prices seem resonable £300 for a SS manifold + you will get
a quality product (I know I'm biassed, building an Indy) worth a phone call!
|
|
Fred W B
|
posted on 5/4/05 at 01:42 PM |
|
|
I am just going through this myself, to make some "up and over" equal length manifolds on a Rover V8.
In my limited experience (see below) I think it would be very difficult to make a pattern acurate enough to get a good result. I would make a manifold
for a mate, but only if he could make the complete car available
What I did:
Bought 90 deg mandrel bends in 38 x 1.6 mm mild steel.
Had head flanges laser cut, so that pipes are fitted with a butt joint to flange.
Bolted flanges to head with wood plugs fitted sticking out of flanges to give me a positive, but movable location for the first bend.
Drew circles on plank of wood the same diameters as inside and outside radius of mandrill bends.
Marked off angles 15, 30, 45 etc, on circles to use as a template to ensure I always cut the bends true to the pipe bore.
Made up first pipe for #1 cylinder as this had longest straight section by tacking elbows, cut elbows and straight pipes together. Try to cut to exact
angles where possible.
Cut #1 pipe to desired length, using calculated length along mean pipe radius to determine total length (straight length+x deg+x deg etc).
Now that position of collector is established, by trail and error join #2 flange to collector, by joining bends in more than one orientation where
necessary.
Don't cheat by cutting joining planes not perpendicular to pipe bore.
I found it easiest to work from rear to head, and keeping the flange to pipe joint loose till the last join.
Repeat for #2,#3 and #4 pipe.
Depending how keen you are on keeping the pipe spacing more or less consistent and parallel, this can drive you crazy.
I found it helped a lot to make some square frames from flat bar to fit around the 4 pipes where they ran parallel, to keep them in position while
tacking bends
Once all pipes are tacked up, remove from flanges again.
Weld up all pipes fully, using TIG if possible, or MIG.
Metal finish if required or desired
Reassemble manifold, and do final head flange to pipes and collector welds. Remember to fit closing plate between pipes at collector.
Now I just have to do the other side............
Cheers
Fred WB
[Edited on 5/4/05 by Fred W B]
|
|
NS Dev
|
posted on 5/4/05 at 02:26 PM |
|
|
Sounds quite a good process, I also have found it easier to build the manifold to fit than try and make a pattern, but only done it on a 4 cyl! Also
had a couple of slightly less than ideal joins where as you said, the joins were not quite perpendicular to the pipe bore!
|
|
907
|
posted on 5/4/05 at 04:00 PM |
|
|
quote: Originally posted by NS Dev
A very good point 907!!!
What's you opinion (as you're the expert in this area) on building a decent exhaust manifold using hygienic stainless tubing?
I am worried about the number of welds, as there will be a lot of bends to get the lengths right etc.
Hi.
Don't know about the expert bit. I'm just a simple engineer.
Yup, it's a good way to fab an exhaust, and as you say, build it as you go.
The outlets on my Lotus head are oval, 25x40mm so I used 1 1/2"pipe for the manifold.
Four pipes into a colector, then 2" from there on.
I havn't got a pic of a complicated dairy bend exhaust, but the pic below gives an idea.
It's for a 1600 c/f with the can mounted under the clamshell wing.
Paul G
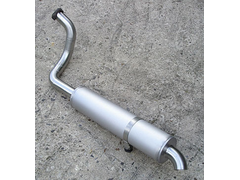 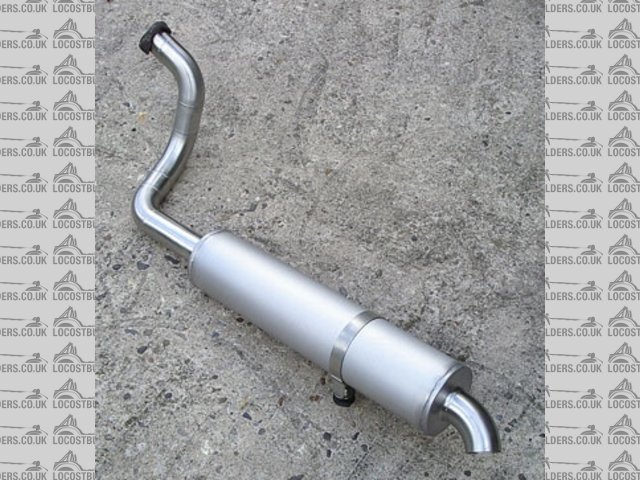 Rescued attachment lotus exhaust 001s.jpg
|
|
NS Dev
|
posted on 5/4/05 at 06:59 PM |
|
|
I just need to get the hang of filler rod control with the TIG, which is tricky when it's not my welder!
You may be "just an engineer" but I am impressed by your fabrications!
Do I "need" to back gas the TIG welds or will they be ok (as in not crack and be gastight) without backgas? (I know they look messy on the
back done this way but it saves a lot of time if I can do without!)
|
|
907
|
posted on 5/4/05 at 07:55 PM |
|
|
quote: Originally posted by NS Dev
I just need to get the hang of filler rod control with the TIG, which is tricky when it's not my welder!
You may be "just an engineer" but I am impressed by your fabrications!
Do I "need" to back gas the TIG welds or will they be ok (as in not crack and be gastight) without backgas? (I know they look messy on the
back done this way but it saves a lot of time if I can do without!)
Hi again,
First of all... Your easily impressed
I use 1mm filler wire, on little welds it's less "blobby".
I always back my welds. With no backing the metal tends to be "stodgy".
It flows so much better with a bit of argon behind it.
I use a 2" disc of metal with the argon line through the middle, and hold
it on the end of the pipe with masking tape.
A disc on the other end with a 4mm hole.
My argon regulator has a tee with two flow meters attached permanently.
Once set up, it realy is no hassle.
HTH Paul G
|
|