RazMan
|
posted on 15/12/05 at 02:46 PM |
|
|
Fitting an electric water pump
As the V6 Duratec has got a reputation for breaking water pumps I decided to cut it out altogether and fit a
Davies, Craig EWP® Electric Water Pump
Apparently it will even give me a sizeable power boost too and I now wonder which layout would be best for my middy.
Option 1: Instal the pump close to the front mounted radiator
Option 2: Install the pump in the engine bay
I've also got to tee the cabin heater (yeah I'm a wuss) pipes in somewhere. Ideally these would come off the rad on an electric valve.
The original takeoff was straight from a water jacket around the oil filter but I have had to remove this to incorporate the EWP.
Your comments would be appreciated
Cheers,
Raz
When thinking outside the box doesn't work any more, it's time to build a new box
|
|
|
Prez
|
posted on 15/12/05 at 03:00 PM |
|
|
How much do those things cost?
|
|
RazMan
|
posted on 15/12/05 at 03:06 PM |
|
|
I bought the pump and 'intelligent' controller for £240 in post. A bit pricey but the standard water pump is also not cheap. According to
their blurb I should see an extra 20 horses too ....... which is nice.
Cheers,
Raz
When thinking outside the box doesn't work any more, it's time to build a new box
|
|
andyd
|
posted on 15/12/05 at 03:07 PM |
|
|
quote: Originally posted by Prez
How much do those things cost?
Click the supplied link in RazMan's post and then click the price list link on the left hand menu.
Andy
|
|
smart51
|
posted on 15/12/05 at 03:17 PM |
|
|
quote: Originally posted by RazMan
According to their blurb I should see an extra 20 horses too ...
UPTO 20 BHP. Which means it is probably less.
Mechanical pumps are drivenby the engine and run at the speed of the engine. They have got to be up to the job of cooling the engine and idle and so
often run furiously fast at high RPM.
An electric pump will probably run at 1 speed. This means that it will use less power at high engine speed leaving you with more at the flywheel.
You can bet that the worst engien they've seen saves 20 BHP and so that's the one they quote.
That said, even if it save 5 BHP, are you going to say no?
|
|
RazMan
|
posted on 15/12/05 at 03:27 PM |
|
|
quote: Originally posted by smart51
An electric pump will probably run at 1 speed. This means that it will use less power at high engine speed leaving you with more at the flywheel.
You can bet that the worst engine they've seen saves 20 BHP and so that's the one they quote.
That said, even if it save 5 BHP, are you going to say no?
The controller matches the pump speed to the engine temperature - very slow during warm-up getting progressively faster at full working temperature. I
agree, their figures are probably biased (but based on a smaller engine) but any extra power is welcomed - I've seen some tuners pay 4 figure
sums on their engines and get similar power gains
Cheers,
Raz
When thinking outside the box doesn't work any more, it's time to build a new box
|
|
02GF74
|
posted on 15/12/05 at 03:35 PM |
|
|
quote: Originally posted by smart51
Mechanical pumps run at the speed of the engine. They have got to be up to the job of cooling the engine and idle and so often run furiously fast at
high RPM.
An electric pump will probably run at 1 speed. This means that it will use less power at high engine speed leaving you with more at the flywheel.
it's never as simple as that. at high engine speed you wold be getting a lot of farced air through the radiator so eb ableto shift heat out
quicker. at low speed or standstill when idling, you have next to no forced air cooling so need a fan and water flow would be low.
electric pump will address both of these problkems as it will djustthe flow i.e. pump speed according to the need.
I'd be very surpsised if the new fangled electronics does not run the pump at variable speed, ^^^^^^^ RazMan beat me to it! even if it
doesn't will be using a thremostat to control the flow according to demand.
they are a pricey; I have considered using a fan or some other motor to drive the water pump pulley via a fan belt in a similar way but it never got
much further than that; should be doable for about £20.
[Edited on 15/12/05 by 02GF74]
just thinking aloud about the power gains. A human being produces less than 1 bhp but put one on a stationary bike and gear it up to drive a water
pump to get the same rate as in a car and I think that is doable; I can't imagine it requires 20 ponies, even 1 ickle shetland pony should do
it. dunno.
[Edited on 15/12/05 by 02GF74]
|
|
02GF74
|
posted on 15/12/05 at 03:44 PM |
|
|
quote: Originally posted by RazMan
The controller matches the pump speed to the engine temperature - very slow during warm-up getting progressively faster at full working temperature.
Does the pump have a facility to run on after the engine has stopped to allow even cooling down after a hard blast?
That is another benefit of non engine driven pumps.
|
|
RazMan
|
posted on 15/12/05 at 03:57 PM |
|
|
quote: Originally posted by 02GF74
Does the pump have a facility to run on after the engine has stopped to allow even cooling down after a hard blast?
That is another benefit of non engine driven pumps.
Yep, and that feature was the one that finally convinced me. My old Nissan (which was fairly highly tuned) used to boil and fizzle after a track
session and I often wished I could keep the water circulating and not just the rad fan.
If the controller is given a permanent power supply it will only cut off when the engine is fairly cold.
[Edited on 15-12-05 by RazMan]
Cheers,
Raz
When thinking outside the box doesn't work any more, it's time to build a new box
|
|
ChrisGamlin
|
posted on 15/12/05 at 10:47 PM |
|
|
I would do a lot of research into the "Craig David's" before fitting one in order to make things more reliable!! They are used a
fair bit on bike engines when people fit dry sumps because they use the mechanical pump drive to drive the dry sump pumps, and they have a reputation
for being fairly cheaply made (although not to buy) and failing quite often - I have heard of them failing within a few hundred track miles so I
certainly cant see it being more reliable than an OEM Ford part even if they do have a reputation for unreliability (relative to other cars which have
water pumps that last 150k miles maybe).
Also, I really wouldnt believe the power gains claimed, if a water pump really took 20bhp to drive it then all cars would have electric pumps. A
friend has one on his dry sumped Hayabusa and it put out the same power on the rollers as any other stock busa would.
[Edited on 15/12/05 by ChrisGamlin]
|
|
RazMan
|
posted on 15/12/05 at 11:02 PM |
|
|
I was under the impression that they are quite reliable. I have read a few reviews and they were regarded as 'the next big thing' but
perhaps their longevity has yet to be proved. I think they have a two year guarantee which is reassuring.
They also did a rolling road test on a 2.0 Duratec and achieved a 7-10 hp gain and 5% fuel saving when compared to the same engine with a conventional
water pump fitted. Quite a bit smaller than the 20hp claimed by the distributor but significant none the less.
I suppose time will tell .... coz mine arrives tomorrow
Cheers,
Raz
When thinking outside the box doesn't work any more, it's time to build a new box
|
|
MikeRJ
|
posted on 16/12/05 at 12:14 AM |
|
|
I have to admit, I find even 5bhp a surprisingly large amount of power to drive a small water pump. Perahps they tested it with the cooling system
full of treacle?
|
|
02GF74
|
posted on 16/12/05 at 10:07 AM |
|
|
quote: Originally posted by MikeRJ
I have to admit, I find even 5bhp a surprisingly large amount of power to drive a small water pump. Perahps they tested it with the cooling system
full of treacle?
it depnds on the test conditions.
engine driven water pumps, as has been said, is drawing power in proprotion to the engine speed not to the cooling requirement.
an electric pump operating in the same way as a mechnicla one is going to be less efficient; you mechnically drive an alternator that produces
electricity to drive an electric motor and there are losses in the conversion to electicity and then back to machical rotation
but you don't use the electric pump the same way - that is where the potential not to waste power comes from.
I don't think you will get problems. if I could justify the cash, I too would look to fit one.
[Edited on 16/12/05 by 02GF74]
|
|
bimbleuk
|
posted on 16/12/05 at 10:09 AM |
|
|
Not quite up there with an LMP car but I did fit one to a supercharged mk1 MR2.
It worked quite well for the time it was fitted and gained 5BHP on the rollers.
|
|
sebastiaan
|
posted on 16/12/05 at 06:32 PM |
|
|
quote: Originally posted by tadltd
As Prodrive discovered, they do release more engine power because they eliminate the parasitic losses associated with an engine driven pump -
it takes engine power to drive any ancillary (e.g. alternator , AC compressor, supercharger, power steering pump [hence electric power
steering], water pump, etc.), so if you can eliminate one of these power drains you claw back power. A water pump can drain a LOT of power when the
engine is operating at high speed.
Erm... where do you s'pose the electricity to run the pump on comes from?
It's an efficiency and usage matter. although the electric pump / alternator / pulley drive system will probably run at a lower efficiency then
the mechanical pump / pulley drive system will, the "intelligent" use of the electric pump could very probably result in a lower net power
usage at high engine speeds.
|
|
RazMan
|
posted on 16/12/05 at 07:43 PM |
|
|
It is the intelligent use that is the key. As other people have said, the mechanical water pump can only be a design compromise - it has to provide
enough flow for all conditions regardless of the engine's true needs. A hyperthetical case for example, when the engine is redlining on the
track the pump is absorbing a suprisingly large amount of power to operate at a ridiculously high flow rate. The electric pump will often operate
after this power surge as it monitors the heat output and not the power output. Therefore (taking things to the extreme) the engine is able to
produce more power when required and can cool down during braking.
Obviously the power required by both systems has to come from the engine, and the efficiency ratios are quite different, but the real difference is
when the power is absorbed.
Cheers,
Raz
When thinking outside the box doesn't work any more, it's time to build a new box
|
|
ChrisGamlin
|
posted on 17/12/05 at 04:25 PM |
|
|
quote: Originally posted by RazMan
I was under the impression that they are quite reliable. I have read a few reviews and they were regarded as 'the next big thing' but
perhaps their longevity has yet to be proved. I think they have a two year guarantee which is reassuring.
They also did a rolling road test on a 2.0 Duratec and achieved a 7-10 hp gain and 5% fuel saving when compared to the same engine with a conventional
water pump fitted. Quite a bit smaller than the 20hp claimed by the distributor but significant none the less.
I suppose time will tell .... coz mine arrives tomorrow
Yep, Im only going on a couple of riend's experience plus a few other things Ive seen said about them by a couple of drivers who run them in the
RGB (Bike engine'd race series), no doubt some are reliable but some clearly arent, and as the reason you seemed to be fitting it was to improve
reliablilty, I thought it relevent to mention.
Just to give you an idea of how I came to think they aren't up to much, one of my friends who runs one on his Westie is on his third pump in
about 4 years (equates to probably no more than 6-8k miles). Another friend is still on his first, but says it now makes a load of noise after about
6k miles, and one of the guys in the RGB had one sieze solid which blew off a hose and spat him off on a high speed corner. As to Prodrive fitting
two to a 550LM, I have no doubt that they throw things like that away after most races anyway so certainly wouldnt be testing long term durability,
and I wonder why they fitted two......
As to the reviews, if you have a look at this then it may explain why there are
only favourable reviews out there
[Edited on 17/12/05 by ChrisGamlin]
|
|
RazMan
|
posted on 17/12/05 at 09:51 PM |
|
|
Agreed, it sounds a bit fishy when they say
"As a courtesy, we showed Davies Craig the test results that we had found.Unfortunately, because of their responses, we now feel that we
cannot bring these stories to you.Thinly veiled threats of legal action from large companies can do that.....
"
This review was over five years agobut to be fair, they might not have been able to publish their results for any number of reasons. Having
said that, I still can't find any bad reviews for the EWP and everything I've read seems to be very favourable.
It's worth noting that the box I received yesterday states in big letters "Generation III with Ceramic Seal" so maybe they HAD a
quality issue in the past and have now revised the design - a lot can happen in five years. It also clearly states a two year guarantee applies which
in my book says they must be confident in their product.
[Edited on 17-12-05 by RazMan]
Cheers,
Raz
When thinking outside the box doesn't work any more, it's time to build a new box
|
|
Fred W B
|
posted on 17/12/05 at 10:05 PM |
|
|
In reply to the original question, I put mine as low as possible, and close to the engine, connected to push first into the motor, and the motor
outlet goes to the rad.
The bottom feed from the header tank goes into a T just before the water pump to ensure constant head of water at the pump. I also connected a top
bleed from the rad to the top of the header.
The system self bleeds perfectly and seem to work well, although I have only conducted idle tests so far.
Cheers
Fred WB
|
|
RazMan
|
posted on 17/12/05 at 10:49 PM |
|
|
Excellent advice Fred - that's exactly the info I need to design my cooling setup, even if if it did take 20 posts to get there
The only thing I don't quite understand is....quote: Originally posted by Fred W B
I also connected a top bleed from the rad to the top of the header.
Are you talking about a middy setup? My rad is over 2 metres from my engine & header tank - do you mean a small hose installed between the two?
Also my Golf rad doesn't have a cap and I was just going to put a bleed valve in the top hose to avoid airlocks. Due to space limitations I was
hoping to use the header tank as a combined expansion tank by half filling it - or am I asking for trouble?
[Edited on 17-12-05 by RazMan]
Cheers,
Raz
When thinking outside the box doesn't work any more, it's time to build a new box
|
|
Browser
|
posted on 18/12/05 at 10:00 AM |
|
|
OEMs can be notoriously slow at adopting new ideas or changing traditional ways of doing things, look how long it took Ford and Vauxhall to start
fitting 5 speed gearboxes to all of their cars despite the euoropean and Jap stuff having had it as standard for years.
Maybe the Davies Craig unit has reliability issues, these will probably be cured. And if Bosch have started making them for BMW that can only be good
news for Locosters as it means scrappies will start getting them in They will probably appear on production cars over the next 5-10 years, as
electric power steering pumps are starting to do now. With ever-tightening emissions laws the ability to speed engine warm-up times has to be
attractive for manufacturers.
Remember, when someone else says they've had reliability issues and blames a piece of equipment you have top assume they fitted it correctly and
ran it correctly. People are wonderful for blaming new kit for not working when actually it was because they didn't read the manual or fitted it
hamfistedly/incorrectly.
I'll stick with the mech pump on my Zetec for its initial build, then look at a D.C. when I've some spare pennies.
|
|
RazMan
|
posted on 18/12/05 at 02:22 PM |
|
|
Here's my draft layout - the heater will be fed by a single 15mm pipe directly from the pump (as there is no thermostat)
Any suggestions?
  Rescued attachment Water Pump diagram.jpg
Cheers,
Raz
When thinking outside the box doesn't work any more, it's time to build a new box
|
|
Fred W B
|
posted on 18/12/05 at 02:48 PM |
|
|
Raz man - Yes, the bleed is from the top of the rad all the way back to the top of the header tank.
You can see it in some of the photos in the thread link below, as I posted in your thread re alloy/rubber pipes.
I also used a swirl pot , with the top bled back to the header tank.
This layout is as recommended by Carrol Smith, in Prepare to Win and Engineer to Win (if anyone else has those books did you notice how the two
diagram's differ? - seems Carrol changed his mind between writing the two books)
Most important point - put the header tank as high as possible. The header tank cap is the only opening I have in the system.
Another point that that he makes, and that makes sense to me, is to have a restrictor in the engine outlet, to keep the block pressure up. On most
engines this is usually the thermostat, so I have retained mine, but with three 6 mm holes drilled in it to allow some flow when it is closed.
I have spent quite a lot of time on the net researching re the DCWP, and for every report you see that has used the DCWP successfully, you will find 5
that state that they know of, or have heard of, or once met a bloke who, had a problem with one. But never first hand knowledge on problems. So will
see for myself once on the road.
Cheers
Fred WB
http://www.locostbuilders.co.uk/viewthread.php?tid=30565
[Edited on 18/12/05 by Fred W B]
|
|
tadltd
|
posted on 18/12/05 at 03:01 PM |
|
|
The feed should go to the top of the radiator, and the heater 't'd' into the feed (to get the most heat from the coolant). The
heater will also act as a small heat exchanger meaning there's less heat in the coolant at the radiator.
Best Regards,
Steve.
www.turnerautosport.com
|
|
RazMan
|
posted on 18/12/05 at 05:46 PM |
|
|
Fred, I know that Davies Craig recommend taking out the thermostat when using their pump but the heater will probably take ages to warm up so I was
considering inserting one in line too, also with some extra holes, to keep some flow going. Now you mention it, it makes sense to keep some block
pressure so it looks like a thermostat is a good idea all round.
The header tank will go in almost the same position yours is mounted and I will incorporate the bleed tube which also makes good sense. I'm not
sure about the swirl pot so I will see how things go and test the system when the car is running.
Steve, I was under the impression that feeding the top of the rad will encourage air locks. My diagram shows it fed from the bottom with the heater
tee'd from the pump to maximise on pressure to get the heater warmed up quicker (it's a theory anyway) The Duratec has a separate water
jacket around the oil filter which I have taken out of circuit for simplicity but I might re-use it if I feel the need - I would put this in the
circuit between pump and heater to get as much heat as possible, shutting it off with a valve (also in the feed) when not required. I can then use the
heater for cold air flow in the summer.
Here's my revised version - now in glowing colour
[Edited on 18-12-05 by RazMan]
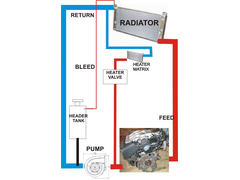  Rescued attachment Water Pump diagram2.jpg
Cheers,
Raz
When thinking outside the box doesn't work any more, it's time to build a new box
|
|