RazMan
|
posted on 14/2/07 at 11:35 PM |
|
|
Induction Choice
As my middy has the intake smack in the middle of the engine bay it is sucking in hot air which is obviously not good for power. I am looking at
ducting fresh air in to improve the situation but which of these options would be the best?
Option A - Short pipe (100mm) from throttle body to air filter with long ducting pipe pointed at the air filter blowing in fresh air
Option B - Long pipe (about 1 metre) direct to air filter which is in the cold air stream.
Are their any advantages with either system? I should add that the throttle body is feeding a plenum and is not going direct to the cylinders.
Discuss
[Edited on 14-2-07 by RazMan]
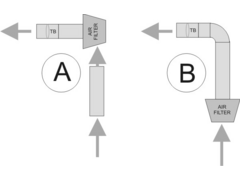  Rescued attachment Induction diagram.jpg
Cheers,
Raz
When thinking outside the box doesn't work any more, it's time to build a new box
|
|
|
phoenix70
|
posted on 14/2/07 at 11:54 PM |
|
|
I would say option B, the air flow should be more settle by the time it reaches the airflow meter.
No science to back this up but my opinion
Scott
|
|
macnab
|
posted on 15/2/07 at 01:29 AM |
|
|
or option C a big scope like an F1 behind your head, hmmm tasty
|
|
smart51
|
posted on 15/2/07 at 09:21 AM |
|
|
You might be better off with A. An elbow in a pipe lin in B causes a reduction in airflow. The sideways filter in A can draw in air from all
sides.
Here is a diagram coutesy of JAG showing K values for various pipes. The lower the K value the better. The top right box shows that an elbow whose
radius is 4x the tube diameter is OK but a tight radius is awful.
|
|
BenB
|
posted on 15/2/07 at 09:56 AM |
|
|
I'd do plan B but make the ducting to the filter as big as possible to reduce loses. The TB to filter ducting would only need to be normal size
(ie TB inlet) as long as it wasn't excedingly long...
|
|
Duncan_P
|
posted on 15/2/07 at 10:01 AM |
|
|
Personally, i would go with B if it is going to mean that you get a colder intake charge. Do you know how hot the air is going into you intake?
if i remember rightly (dont quote me) you'll see about a 1% increase in HP for every 10 degree drop in charge temp due to more air going into
your engine (colder therefore denser).
But routing is going to get tricky if you run individual pipes for each Throttle Body...... I would maybe start thinking about an air box
|
|
RazMan
|
posted on 15/2/07 at 11:57 AM |
|
|
quote: Originally posted by Duncan_P
But routing is going to get tricky if you run individual pipes for each Throttle Body...... I would maybe start thinking about an air box
The pipe is from the air filter to the plenum via the single TB
If I make two bends of 135° it should make less friction than 90° bends.
I think I will go for that then - it will allow me to mount the air filter in the cold airflow. The longer pipe certainly give the induction roar a
much deeper sound too
Cheers,
Raz
When thinking outside the box doesn't work any more, it's time to build a new box
|
|
timf
|
posted on 15/2/07 at 12:08 PM |
|
|
quote: Originally posted by RazMan
The pipe is from the air filter to the plenum via the single TB
If I make two bends of 135° it should make less friction than 90° bends.
I think I will go for that then - it will allow me to mount the air filter in the cold airflow. The longer pipe certainly give the induction roar a
much deeper sound too
if you go for option b look for some wrapable pipe insulation to insulate the pipe from the surrounding heat in the engine bay
A prisoner of war is a man who tries to kill you and fails, and then asks you not to kill him."
- Sir Winston S. Churchill, 1952
|
|
bigbravedave
|
posted on 15/2/07 at 12:41 PM |
|
|
Im a powertrain design engineer by trade, without going into it in a mamouth way, you want to keep your intake ducting as short as possible with the
coldest air feed possible, as the engine sucks air, the greater the intake restriction the greater the pressure drop and the thiner the supplied air,
you also want to keep all the ducting and the airbox as cool as possible keeping it away from the hot bits, with ever increasing under bonnet temps
its a compromise.
|
|
RazMan
|
posted on 15/2/07 at 04:18 PM |
|
|
Dave - Are you saying that option A would be the best idea then? It has the shortest intake path but it would have cold air ducted in its direction
and not a direct feed. This would obviously mean that it would still take in some warm air along with the cold.
Option B would have the coldest air but the longest intake path.
I'm confused now
Here's a pic to clarify - you can just see the air filter on the end of the alloy pipe. I was thinking about extending the pipe into the side
pod (under the visible filler cap), out of the way of the dirt thrown up by the wheel.
[Edited on 15-2-07 by RazMan]
Cheers,
Raz
When thinking outside the box doesn't work any more, it's time to build a new box
|
|
MikeR
|
posted on 15/2/07 at 04:28 PM |
|
|
Couldn't you put the air filter right next to the engine but put it in a large box, then have a couple of cold air feeds to the box?
multiple feeds would supply lots of air, the box would mean the filter only gets cold air & a short path to the throttle body.
|
|
DIY Si
|
posted on 15/2/07 at 05:01 PM |
|
|
I'd just extend the pipe. I thought having a reasonable length of inlet was good for torque, but I'm no professional. Could you just
extend the pipe in a straight line? Or as said, go up and not a roof vent thing, like the NSX?
“Let your plans be dark and as impenetratable as night, and when you move, fall like a thunderbolt.”
Sun Tzu, The Art of War
My new blog: http://spritecave.blogspot.co.uk/
|
|
martyn_16v
|
posted on 15/2/07 at 08:34 PM |
|
|
quote: Originally posted by DIY Si
I thought having a reasonable length of inlet was good for torque
Pulse tuning? That only applies from the back of the inlet valve up to the first big change in runner diameter/obstruction, so in this case it'd
be the distance from head to plenum.
|
|
DIY Si
|
posted on 15/2/07 at 08:40 PM |
|
|
I thought it went further to include the entire system, bit like tuning an air box. Or the thing about a column of moving air having a certain amount
of momentum, thus causing a bit of a ram affect type joibbie. As said though, I'm no professional on these fairly complicated things.
There's no hammer involved!
[Edited on 15/2/07 by DIY Si]
“Let your plans be dark and as impenetratable as night, and when you move, fall like a thunderbolt.”
Sun Tzu, The Art of War
My new blog: http://spritecave.blogspot.co.uk/
|
|