Mike Wood
|
posted on 28/2/11 at 11:15 PM |
|
|
Brazing Locost chassis - why not?
I thought one of the advantages of use brazing rather than MIG welding is that it can be easier to produce a dimensionally accurate tube chassis, as
less heat distortion, ease of tacking and making complex joints, as well as the ability to repair. Also a brazed chassis should have less welding
stress built in (and in theory such welded, not brazed, structures need heat treating to remove it). Do need accurate close gaps in joints for brazing
though.
Apart from ease of using MIG, the cost of kit and what Champion's book suggests, I've wondered why all Locost chassis are all welded not
brazed? This is unlike all Lotus and Caterham 7s made by Arch Motors (until recent metric chassis made by Caged on a computerised welding jig) as well
as Mallocks and other steel tubed racing cars, including homebuilt 750 Formula cars. Maybe cheaper for Locost chassis manfucturers to use MIG?
Is the art of brazing is lost, and no-one wants a live flame or exciting gases in their garage?
Cheers
Mike
[Edited on 28/2/11 by Mike Wood]
|
|
|
Steve Hignett
|
posted on 28/2/11 at 11:24 PM |
|
|
LOL, Think you have answered your own question (about three times!!!)
I need to learn how to Braze and Tig...
[Edited on 28/2/11 by Steve Hignett]
|
|
mark chandler
|
posted on 28/2/11 at 11:30 PM |
|
|
Good enough for E type jags
MIG is used as its fast = cheap
TIG is used as its very available although relatively expensive and joins thick to thin with ease.
Brazing is an art, if you can no reason not to.
|
|
stevebubs
|
posted on 28/2/11 at 11:32 PM |
|
|
http://www.locostbuilders.co.uk/viewthread.php?tid=1181
|
|
Wadders
|
posted on 28/2/11 at 11:37 PM |
|
|
Doubt the chassis from Arch would be brazed in the accepted sense, more likely to be bronze welded
using a gas fluxer, far more chance of distortion in untrained hands than mig welding,and a damn sight more expensive
and slower. Only worth the effort if you are using Reynolds tube or similar IMHO
Al
|
|
r1_pete
|
posted on 1/3/11 at 07:58 AM |
|
|
quote: Originally posted by mark chandler
Good enough for E type jags
Not much brazing on E Types, no more than similar cars of the period, dorr skin ends and wing edges....
Pity because I do quite a lot of brazing, especially large to small components.
I Know from personal experience: 
 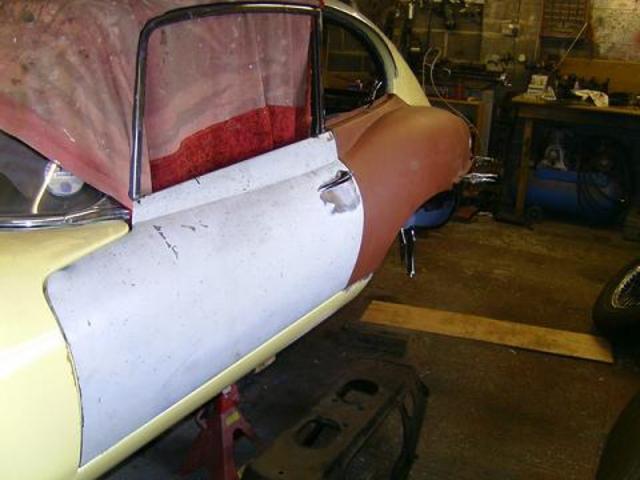 back wing
[Edited on 1/3/11 by r1_pete]
|
|
MikeCapon
|
posted on 1/3/11 at 08:09 AM |
|
|
Having been a brazer in the dim and very distant past perhaps I can offer a bit of info.
There are two distinct methods of brazing steel both of which can be acheived with either an in line fluxer, fluxed rods or the old flux powder in a
tin that you dip the rods into from time to time.
Method 1 The assembly is heated up all over until dull red. The rod (and flux) is then introduced and immediately flows into the gaps via the
capillary action mentioned above. This method requires close fitting components and is relatively weak as there is no fillet of brass to spread the
load.
Method 2 The joint is heated locally and as soon as possible the rod and flux are introduced. Once started the braze is continued along the joint,
using the movement of the torch and the rod to create a fillet of brass. Properly done this is a very strong joint and aesthetically is probably one
of the most pleasing types of joint to look at, along with a good tig weld.
Method 2 is also a great deal more tolerant of gaps between components. As for its suitability for a chassis I would be happy with it, done correctly.
It is also more tolerant of vibration than a welded joint.
In the past I have made swing arms, repaired and modified chassis on countless race bikes without ever having a problem.
Cleanliness before brazing is the key to a good joint. Any impurities in the joint will show up immediately. It is very easy to look at a brazed joint
and determine how well it has been done.
It does take a bit of practice though and i would estimate that the actual making of a joint would take around twice the time of a mig. It is still
quicker then gas welding though but that is another story....
|
|
Humbug
|
posted on 1/3/11 at 08:22 AM |
|
|
Without knowing anything about the techniques, from a layman's point of view I would have thought that joining two bits of steel with brass
wouldn't be as strong as welding which in my simplistic understanding is like melting the edges of the steel and filling the gap with more
steel?
|
|
David Jenkins
|
posted on 1/3/11 at 08:37 AM |
|
|
quote: Originally posted by Humbug
Without knowing anything about the techniques, from a layman's point of view I would have thought that joining two bits of steel with brass
wouldn't be as strong as welding which in my simplistic understanding is like melting the edges of the steel and filling the gap with more
steel?
For chassis work you'd use bronze brazing, not brass - an alloy of copper & tin, rather than copper & zinc. Two very different
materials - brass is brittle, but remember that they used to make swords and axes out of bronze a couple of thousand years ago, so that's pretty
tough stuff!
|
|
MikeCapon
|
posted on 1/3/11 at 08:38 AM |
|
|
quote: Originally posted by Humbug
Without knowing anything about the techniques, from a layman's point of view I would have thought that joining two bits of steel with brass
wouldn't be as strong as welding which in my simplistic understanding is like melting the edges of the steel and filling the gap with more
steel?
Valid point Humbug but you need to consider the following.
A joint only needs to be as resistant as the material it is joining and providing a good fillet is created there will be adequate material in place to
achieve this.
Also, a larger fillet will spread the load over a greater area in the tube being joined and will hence be will actually be stronger than a welded
joint with a much smaller, and iregular, fillet.
ETA Sorry David, my bad. I should not have used the word brass when meaning braze, ie proper brazing rod material.
[Edited on 1/3/11 by MikeCapon]
|
|
40inches
|
posted on 1/3/11 at 09:08 AM |
|
|
Back in the day, when MIG/TIG welding was unheard of, Silicon bronze welding was the weapon of choice when building Bike and car frame/chassis, and as
far as I know still is at Caterham. Mig/Tig became popular due to it's speed in comparison to Bronze welding.
Note: Bronze welding is NOT the same as Brazing, and is much stronger without the need for close joints.
An example of Bronze welding
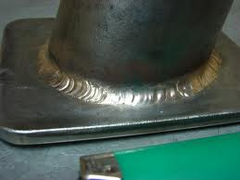 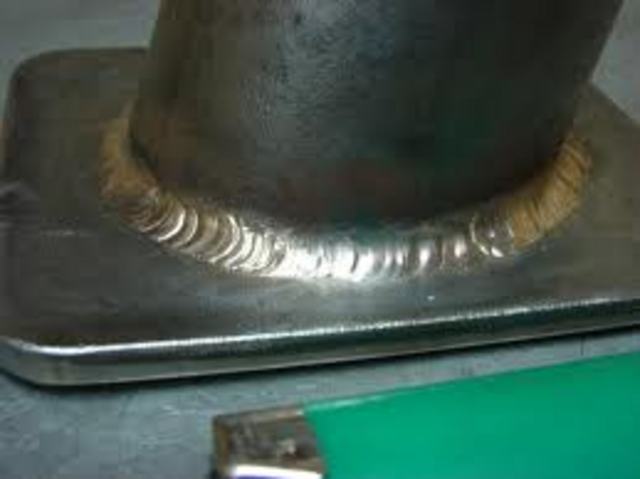 Description
|
|
ashg
|
posted on 1/3/11 at 09:23 AM |
|
|
i think the simple fact is that its too easy to mig it.
i migged and tigged my chassis when i made it. i have done brazing in the past and had good results but I don't think I would be confident to
do a whole chassis with it.
Anything With Tits or Wheels Will cost you MONEY!!
Haynes Roadster (Finished)
Exocet (Finished & Sold)
New Project (Started)
|
|
A1
|
posted on 1/3/11 at 03:00 PM |
|
|
I thought caterham did something using bronze... isnt bronze welding less brittle (for want of a better word) than a welded joint?
|
|
Bare
|
posted on 1/3/11 at 05:24 PM |
|
|
Brazing
Can be v good in skilled hands. I believe 'most' available Brazing rods are currently of silcon /bronze, based on recent perusing of
welding materials/supplies data sheets. Gas torches are not so inexpensive and consumable Gases are not free either. Brazing is not a $$ saving
method.
MIG is quite easy to learn/do :-) Cheapish Kit too.
TIG is V good, but very slow and tedious, also demanding good skills and the equipment required is surprisingly pricey
|
|
smithwrecker
|
posted on 10/3/11 at 05:33 PM |
|
|
I used to be an M.O.T. tester in the '80s and we had a memo' round from the ministry stating that "brazed repairs to structural
areas was no longer acceptable for M.O.T. purposes" Always loved to braze myself, made for a lovely neat job but stopped after we had the memo.
Perhaps that's why the chassis is not brazed?
|
|
britishtrident
|
posted on 10/3/11 at 05:58 PM |
|
|
quote: Originally posted by A1
I thought caterham did something using bronze... isnt bronze welding less brittle (for want of a better word) than a welded joint?
More or less yes.
Bronze welding has less effect on the heat affected zone metalurgy of the parent metal, welds usually fail in the heat affected zone.
However for bronze welding to be sound the surface prep must be first class.
[I] “ What use our work, Bennet, if we cannot care for those we love? .”
― From BBC TV/Amazon's Ripper Street.
[/I]
|
|
gazza285
|
posted on 12/3/11 at 03:17 AM |
|
|
quote: Originally posted by smithwrecker
I used to be an M.O.T. tester in the '80s and we had a memo' round from the ministry stating that "brazed repairs to structural
areas was no longer acceptable for M.O.T. purposes" Always loved to braze myself, made for a lovely neat job but stopped after we had the memo.
Perhaps that's why the chassis is not brazed?
Brazing/bronze fillet welding is not an acceptable MOT repair as you can get the fillet to stick to rust, so no way to guarantee the strength of the
repair. Fine for chassis building though, just extremely time consuming and expensive, unless you have all the gear already .
DO NOT PUT ON KNOB OR BOLLOCKS!
|
|
907
|
posted on 12/3/11 at 10:00 AM |
|
|
If I may I'll chip in with my 2p.
Although MIG is easy to learn and the quickest method to use it does have one possible problem,
that is, cold start. There are ways round it but something to bear in mind.
Also, another common weld defect is undercut, with TIG or MIG. The smallest amount is a stress raiser
and the possible start of a fracture.
Burn through, easy to get on thin metal, is yet another one. I'm thinking here of wish bones.
The Caterham ones are works of art, and the tube that holds the metalistic bush is delicate to say
the least, a difficult joint to make with out over penetrating and needing a clean up with a die grinder.
These are all things where bronze welding excels, as the O/A flame preheats the joint, and as the
parent metal doesn't melt, the bronze filler tends to flow and produce a large concave fillet that
blends nicely into the tube. A 3 or 4 mm fillet is perfect on a 1.5 (or less) wall tube, and a stress free joint.
In saying this, I tend to reach for whatever process suits that joint.
When getting in to awkward joints even the humble stick rod has its place.
Cheers,
Paul G
|
|
Thailoz
|
posted on 7/3/13 at 07:40 AM |
|
|
The original lotus 7 and early lotus f1 cars were bronze welded using a gas fluxer according to my father who worked for both lotus cars and team
lotus
|
|
mcerd1
|
posted on 7/3/13 at 12:23 PM |
|
|
quote: Originally posted by MikeCapon
quote: Originally posted by Humbug
Without knowing anything about the techniques, from a layman's point of view I would have thought that joining two bits of steel with brass
wouldn't be as strong as welding which in my simplistic understanding is like melting the edges of the steel and filling the gap with more
steel?
Valid point Humbug but you need to consider the following.
A joint only needs to be as resistant as the material it is joining and providing a good fillet is created there will be adequate material in place to
achieve this.
Also, a larger fillet will spread the load over a greater area in the tube being joined and will hence be will actually be stronger than a welded
joint with a much smaller, and iregular, fillet.
ETA Sorry David, my bad. I should not have used the word brass when meaning braze, ie proper brazing rod material.
just to add to that ^^
steel weld metal is normally not as strong as the parient metal in the tubes/plates you are welding together
put it this way:
1 - a steel with a known chemical make-up thats been produced by rolling down to the correct sizes under controlled temperatures to produce a
controled cristal size to give a predictable strength and toughness
2 - a small puddle of molten metal thats chemistry will depend on how much of the parent metal was melted and how much/what type of filler (aka
welding wire) was used - never mind any impurities - then just leave it out to cool down itself with very limited control over its cristal
structure...
which one do you think is stronger ?
in actual fact the welding wire itself is normally stronger and tougher than the parent metal to make up for some of this
eg. we use E42 class wire at work (for S355 steel) it has an yield strength of 420 N/mm²
the steel has a yield of 355 N/mm² - that all sound great so far but the design strenght for a fillet weld is only 250 N/mm² !!
so you need a decent size of fillet to make up for that....
while we are on the topic - what grades of steel you are welding ?
if you've got steel tubes are they 'hot finished' or 'cold formed' ?
what the spec of the welding wire you've got and does it match the parent materials ?
if you've got 'mild steel' that could still be one of hundreds of grades and qualities:
british mild steel for structural purposes (ie most of the angles, tubes, plates you can buy) is a grade S275 (ie 275 N/mm² )
but european mild is only S235 (235 N/mm² ) and its easy to get in this country these days too
then there is the quaility - its a little suffix on the end of the grade that tells you the toughness that its been tested to for brittle fracture -
it can be untested (ie knowone knows how good it is )
"JR" (tested at +20°C)
"J0" (tested at 0°C)
"J2" (tested at -20°C)
"K2" (tested at -20°C but equivelent to -40°C)
if its passed a lower temperature test then its tougher better steel
(btw - that doesn't mean you can't use JR bellow +20°C, its actually good down to -15°C as long as its no more than 10mm thk for
structural uses)
tubes are most common as S355-J2H in hot-finished or cold-formed (the 'H' on the end doesn't mean Hot, it means Hollow)
but that doesn't mean that you can't get a S235 untested one (common in small size tubes)
cold-form tubes have higher residual stresses and bigger radius corners - neather are good things for strength !
cold form is sold to EN 10219, hot-finish is sold to EN 10210 - given the choice I'd pick hot every time (and from a good supplier with
real certificates)
chances are the locost/haynes books are writen with rubbish quaility steel in mind (I'd have to re-read them to see what the actually say about
steel grades)
so I'd take a good look at the material sizes, thicknesses and strengths/qualities of everything else before I went anywhere near fancy things
like bronze or tig welding
it should be possible to design a chassis that is significantly lighter, just as strong and can take full advantage of bronze weldings benafits if
your very careful about all the grades and quailites involved - in fact I'm sure thats what caterham have done
but saying all that I'm more than happy with my MIG welded Dax chassis
[Edited on 7/3/2013 by mcerd1]
[Edited on 7/3/2013 by mcerd1]
-
|
|
eddie99
|
posted on 7/3/13 at 12:36 PM |
|
|
If you have the skill, i didnt see a reason not to braze hence our new car is mainly brazed.
http://locostbuilders.co.uk/forum/15/viewthread.php?tid=178467
http://www.elitemotorsporteng.co.uk/
Twitter: @Elitemotoreng
Facebook: http://www.facebook.com/pages/Elite-Motorsport-Engineering/153409081394323
|
NOTE:This user is registered as a LocostBuilders trader and may offer commercial services to other users
|
mcerd1
|
posted on 8/3/13 at 10:39 AM |
|
|
quote: Originally posted by eddie99
If you have the skill, i didnt see a reason not to braze hence our new car is mainly brazed.
http://locostbuilders.co.uk/forum/15/viewthread.php?tid=178467
for the record I think your new chassis looks really good
-
|
|
eddie99
|
posted on 8/3/13 at 04:16 PM |
|
|
quote: Originally posted by mcerd1
quote: Originally posted by eddie99
If you have the skill, i didnt see a reason not to braze hence our new car is mainly brazed.
http://locostbuilders.co.uk/forum/15/viewthread.php?tid=178467
for the record I think your new chassis looks really good
Thanks, its coming along nicely.
http://www.elitemotorsporteng.co.uk/
Twitter: @Elitemotoreng
Facebook: http://www.facebook.com/pages/Elite-Motorsport-Engineering/153409081394323
|
NOTE:This user is registered as a LocostBuilders trader and may offer commercial services to other users
|
designer
|
posted on 8/3/13 at 04:38 PM |
|
|
Done correctly, a properly brazed joint is be as good as a weld.
BUT, the vehicle inspector has no referance to what skill the bloke who brazed it has! There is no visual check as you have with MIG/Tig, and a bad
joint looks just the same as a good one.
|
|
Dualist
|
posted on 8/3/13 at 07:34 PM |
|
|
Brazing is better as it allows a bit of flex.
When Caterham moved production from Arch Motors the chassis were from then on all mig-brazied using a synoptic mig welder as used in the robot
industry.
I would have loved to mig-brazied my chassis but a proper sized reel of wire is over £300
[Edited on 8/3/13 by Dualist]
Rotary build coming soon...
quote: Originally posted by RichardK
I recently discovered that pigs can p i s s sideways when being transported 
|
|