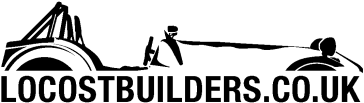
Body using SolidWorks
Cobra289 - 20/9/08 at 10:13 AM
Hi,
I have develop some body works for a locost chassis.
I like the color "Deep Candy Apple Red" so that is the color that I have used.
It is a 100% build in SolidWorks, although working with surfaces in SW is difficult.
See if you like.

mr henderson - 20/9/08 at 10:19 AM
A stunning achievement.
How will the doors open?
Are those lights adequate?
John
gavin174 - 20/9/08 at 10:31 AM
absolulety stunning..
think the rear lights would fall fowl of sva requirements
possibly to far in fron outer edge of car.jpg)
Cobra289 - 20/9/08 at 10:32 AM
quote:
Originally posted by mr henderson
A stunning achievement.
How will the doors open?
Are those lights adequate?
John
Thanks for the compliment.
The door latch needs to be develop but I can say that I have a DAX cobra and the door goes open just by activating a latch at the inside of the car.
Do no see any problem, lots of possibilities.
The light, lamps are adequate, they are the Hella's 50 mm modules, Not the HID bu just the halogen type.
The dimensions of the chassis are the same as the Haynes book of Chris Gibbs so it has a wide [outside the tubes] of 1118 mm
Regards,
Cobra289
Cobra289 - 20/9/08 at 10:53 AM
quote:
Originally posted by gavin174
absolulety stunning..
think the rear lights would fall fowl of sva requirements
possibly to far in fron outer edge of car
Thanks!
The rear lights units are located at the nex dimensions:
Outer unit center line is at 322 mm from the edge of the wheel mudguard.
Inner unit center line is at 516 mm from the same edge of mudguard.
So I think that there isn't a problem.
Regards,
Cobra289
McLannahan - 20/9/08 at 11:08 AM
Looks fantastic! Hats off to your skill in Solidworks!!
blakep82 - 20/9/08 at 11:08 AM
hella 50mm lights? where can i get them?
BenB - 20/9/08 at 11:12 AM
Blimey! Schminky pinky!!!!
Cobra289 - 20/9/08 at 11:12 AM
quote:
Originally posted by McLannahan
Looks fantastic! Hats off to your skill in Solidworks!!
Thanks!
It is not so difficult, the problem is that you need to be persistent to get where you like.
Regards,
Cobra289
Cobra289 - 20/9/08 at 11:17 AM
quote:
Originally posted by blakep82
hella 50mm lights? where can i get them?
I don't know where are you located, but here is a link for information.
Hella 50 mm Modules http://www.rallylights.com/hella/50mm_modules.asp
Regards,
Cobra289
Cobra289 - 20/9/08 at 11:23 AM
quote:
Originally posted by BenB
Blimey! Schminky pinky!!!!
Although I don't know what means your words [expressions], I thank you!
Regards,
Cobra289
Cobra289 - 20/9/08 at 11:51 AM
At certain moment of the design I did open de door and the bonnet.
Just for the looks and to see if there are no interference.
The gearbox MT75 was borrowed from member hellbent345 [Thanks again]
Regards,
Cobra289
BenB - 20/9/08 at 11:56 AM
quote:
Originally posted by Cobra289
quote:
Originally posted by BenB
Blimey! Schminky pinky!!!!
Although I don't know what means your words [expressions], I thank you!
Regards,
Cobra289
Whoops! Didn't spot the location....
http://uk.youtube.com/watch?v=v1iX7AIhV8w&feature=related
designer - 20/9/08 at 01:11 PM
Stunning is the only word for your renderings.
How many yaers has it taken you to get this far with Solidworks?
Cobra289 - 20/9/08 at 01:55 PM
quote:
Originally posted by designer
Stunning is the only word for your renderings.
How many yaers has it taken you to get this far with Solidworks?
Years???? we can talk about months.
At the end of 2007 I did the first work with SW.
Prior to that I have used "LightWave" [nice for renderings but not accurate to construct parts].
If you know AutoCAD it will be not to difficult to jump into SW.
As and old man of 54 years, I can say that I have experiences with 3D software's as PDMS and PDS and that helps.
The important thing is, been persistence, try things ans change a lot.
The first steps of working with SW are easy, just make a 2D sketch and give an extrusion.
With surfaces you work with a lot of 3D sketches and some times are difficult to place at the right spot.
Here is a bunch of screen shots that shows how I did the surface of the body.
Regards,
Cobra289
[Edited on 22/9/08 by Cobra289]
Ivan - 20/9/08 at 02:19 PM
Brilliant work - wish I had patience to develop skills to your level.
irvined - 20/9/08 at 03:50 PM
I love it! The whole hot-rod look in general works, I also really like the front lights.
Cobra289 - 20/9/08 at 04:01 PM
quote:
Originally posted by Ivan
Brilliant work - wish I had patience to develop skills to your level.
Thanks!
Remember "Patience" is the cheapest item in a "Locost" build.
Regards,
Cobra289
mr henderson - 20/9/08 at 04:05 PM
Supposing you wanted to actually build the car, what would be the steps you would use to create the moulds?
John
Cobra289 - 20/9/08 at 04:11 PM
quote:
Originally posted by irvined
I love it! The whole hot-rod look in general works, I also really like the front lights.
Hi!
Thanks!
Get to that shape [idea] was the dificult part of the design.
In particular because to work with surfaces you need to plan a lot, how to do it.
Regards,
Cobra289 [Schiedam not far from Utrecht]
Cobra289 - 20/9/08 at 04:34 PM
quote:
Originally posted by mr henderson
Supposing you wanted to actually build the car, what would be the steps you would use to create the moulds?
John
There are three ways of doing, and all depends of the budget.
- The expensive way is the build a buck in a 5 axis CNC machine.
This way you will get the mold for fabrication of a large series of body's.
- If you want to make a mold, [that you can make corrections and additions] so that you can pull a series of 10 bodies, than you need to work with
wooden sections and cover them with a negative layer of GRP that would be the mold.
- When you plan to make "one-off" [cheap solution for the locost spirit] you make sections [say every 200 mm] than you cut it from 10 mm
plywood [all ready with the support strategy at the chassis]
Then you put the PU of or PVC foam of 6 or 10 mm, between the frames, grind or shave it to your taste and put some layers of epoxy with carbon fibers
or other type of fibers. Needs to say that you need to use a Peel-ply layer to get the nice outer surface.
The inner side of the foam and wooden ribs, should be also cover with a layer of GRP.
The tail-line [largest curvature] needs to be done by thicker PU to get the shape.
After having the shape [basic] you go further with cutting the doors and bonnet an all the holes or recesses that you like to have. [2 mm gap would be
wonderful]
Those parts you need to have some edges, that you can add at this stage.
As you can see from the pictures, the surfaces are easy to shape, even in aluminum [with some craftsman level] The most bended [two directions] part
would be the rear panel .
So the pocket would decide the method to use.
Believe me, the shape as been keep that way, just to be easy to build.
I hope that you can understand my explanations.
Regards,
Cobra289
[Edited on 20/9/08 by Cobra289]
Cobra289 - 20/9/08 at 04:49 PM
Hi,
This picture will illustrate how difficult or easiest, is the basic shape of the body.
The front lamp niche is just an oval pipe that would be layered after the main body is done.
See also the corner area between the top surface and the vertical surface.
I hope that this clears-up a bit my explanation.
Regards,
Cobra289
Triton - 20/9/08 at 07:47 PM
Wicked looking body design mate, think you should make that.
Mark
Cobra289 - 20/9/08 at 08:00 PM
quote:
Originally posted by Triton
Wicked looking body design mate, think you should make that.
Mark
Thanks!
I hope that my son will do the work.
Just now I have posted pictures in blue at the Haynes forum.
Regards,
Cobra289
[Edited on 20/9/08 by Cobra289]
Triton - 20/9/08 at 08:07 PM
An alternative body for the Locost, you have to make it.
Looks cool in Blue but what would it look like in my colour of the month.....pink?
Cobra289 - 20/9/08 at 08:12 PM
quote:
Originally posted by Triton
An alternative body for the Locost, you have to make it.
Looks cool in Blue but what would it look like in my colour of the month.....pink?
The comic "Tony Salazar" say:
"Once I was gay, but I got my turn, I quit!"
I can make it!
Regards,
Cobra289
Triton - 20/9/08 at 08:16 PM

think that told me then...

FUORISERIE - 22/9/08 at 01:52 PM
quote:
Originally posted by Cobra289
At certain moment of the design I did open de door and the bonnet.
Just for the looks and to see if there are no interference.
The gearbox MT75 was borrowed from member hellbent345 [Thanks again]
Regards,
Cobra289
Great Skills and your design is unique and original.
Ciao
Italo
Cobra289 - 22/9/08 at 02:59 PM
Thanks to all for the input and compliments!
Just an improvement of the look of the dip at the bonnet.
I made some slots [cut-outs] to guide some cool air to the hot feet's.
See the pictures.
Regards,
Cobra289
Cobra289 - 25/9/08 at 09:41 PM
Hi,
Here is a set of pictures of the possible hardtop.

Vindi_andy - 26/9/08 at 01:38 PM
IMHO that hardtop version looks great, Can you design a hrad top for a Vindicator family lol
Liam - 26/9/08 at 06:34 PM
Wow!! Awesome stuff!!
That's not actually the solidworks photoworks built-in renderer is it? If it is could you give some tips on what settings etc etc you use to
create results like than in solidworks?
Cheers,
Liam
Cobra289 - 26/9/08 at 07:30 PM
quote:
Originally posted by Liam
Wow!! Awesome stuff!!
That's not actually the solidworks photoworks built-in renderer is it? If it is could you give some tips on what settings etc etc you use to
create results like than in solidworks?
Cheers,
Liam
Hi Liam,
This is a 100% design with SW and the renderings too. I use SW 2007
Nothing has been done outside SW, even the background picture is located at SW directories.
You need to activate the add-in [via tools "add-ins'] the "Photoworks" select the box Start too. So that the next time the SW will
start with the activated Photoworks.
Please choose first an small file, because it requires some power from the PC and I don't know about yours.
OK once you open a file you will see at the left the Photoworks icon at the feature manager and at the tools [top] you will also see the
photoworks.
At the feature manger you click on the icon and you will get:
Scene
Materials
Decals
Lighting
So you can work with those giving to the faces or bodies the material you want.
To get the studio that I use [background] you got to the tool bar and select Photoworks a use the first button "Photoworks Studio" than you
will get a box where you can select the different studios.
The one I use id the "Daytime"
There is a lot to tell but that would extend the response to much, I think that is worth to give a GO and see what happens when you select a
rendering.
Try a box and make it from gold or polished stainless steel or even carbon fibers types.
Regards,
Cobra289