NS Dev
|
posted on 13/5/06 at 10:36 PM |
|
|
5 evenings work + 1 tig welder = pround Nat!!!!
Have to say for the first time in my life I am genuinly REALLY proud of a piece of my own work, so i am going to blow my trumpet now!!
Decent exuast manufacturers quoted me approx £700 for a decent 4-2-1 manifold for my XE.
I bought a load of stainless mandrel mends and tube for £200 (but have used less than half of it so call it £100 worth of materials)
I bought the new TIG that I have been rattling on about for £525 9 days ago,,,,,,,,,,,,,,,,,,
here's my first piece of work::
 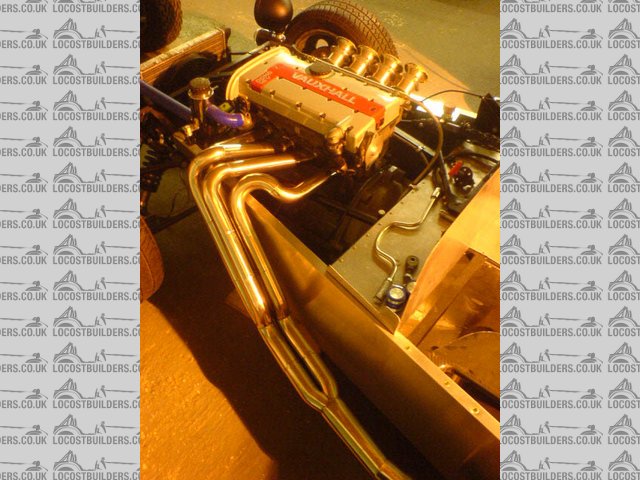 exhaust 2
 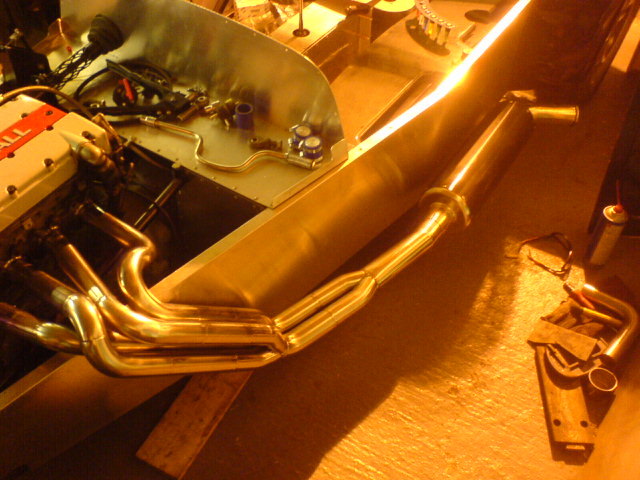 exhaust 3
 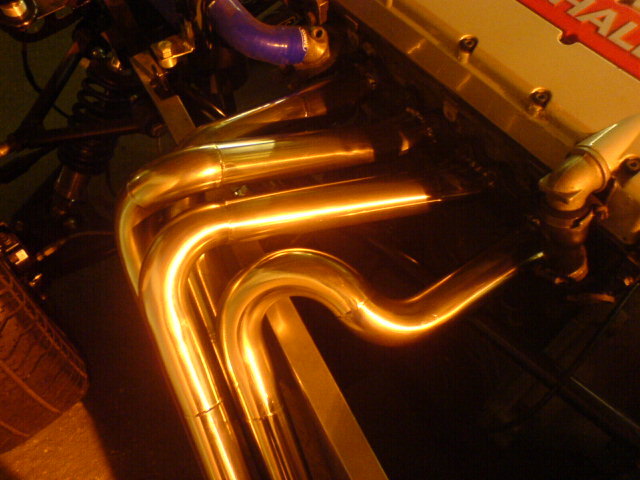 exhaust 1
 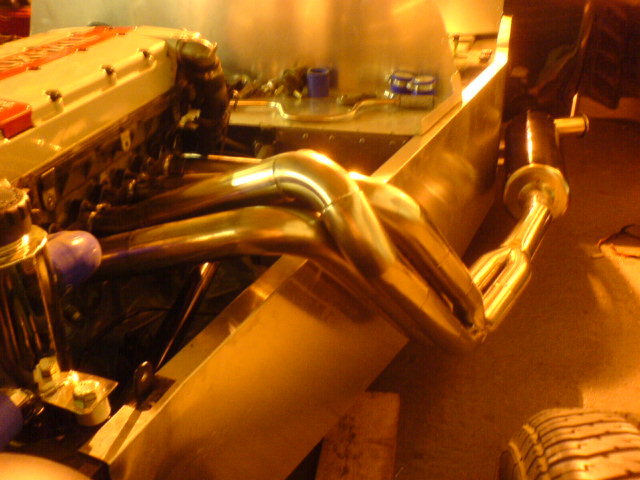 exhaust 4
I'm really chuffed and on this pccasion happy to blow my own trumpet!
Retro RWD is the way forward...........automotive fabrication, car restoration, sheetmetal work, engine conversion
retro car restoration and tuning
|
|
|
DIY Si
|
posted on 13/5/06 at 10:45 PM |
|
|
quote:
I'm really chuffed and on this pccasion happy to blow my own trumpet!
And rightly so sir! Fancy making some of that £525 back?
|
|
andylancaster3000
|
posted on 13/5/06 at 10:45 PM |
|
|
Thats really quite impressive! Going to have to do the same thing not long from now but was wondering a few things. Is stainless welding much harder
then mild welding? Also, where did you buy the bends from?
Cheers,
Andy
EDIT!!: Sorry supposed to say mild welding rather then mig welding! Was a bit late for me!
[Edited on 14/5/06 by andylancaster3000]
|
|
Avoneer
|
posted on 13/5/06 at 11:05 PM |
|
|
Ooo, very nice.
Pat...
No trees were killed in the sending of this message.
However a large number of electrons were terribly inconvenienced.
|
|
NS Dev
|
posted on 13/5/06 at 11:05 PM |
|
|
Stainless welding is just the same as mild steel welding BUT TIG welding is very different to MIG welding!
That manifold was all TIG welded, mig would be fine but nowhere near as neat!
The bends were bought from a place called SDW Light Fabrication:
SDW LIght Fab Linky
really helpful place, with possibly the best lady in the world on the phone, you'll have a right laugh with her!!
They deal with small orders and prices are "negotiable" (obviously within reason, they aren't the sort of place to f*** about!)
cheers
Nat
Retro RWD is the way forward...........automotive fabrication, car restoration, sheetmetal work, engine conversion
retro car restoration and tuning
|
|
DIY Si
|
posted on 13/5/06 at 11:08 PM |
|
|
Fancy making me one when I get that far?
Go on, pleeeaaaassseee?
|
|
NS Dev
|
posted on 13/5/06 at 11:09 PM |
|
|
PS It isn't quite equal length, the 1-4 primaries are the same length as are the 2-3 but there's a slight difference between the two, but
this is no different to any of the systems that I have measured from "major" manufaturers, and should spread the torque a touch as well.
Retro RWD is the way forward...........automotive fabrication, car restoration, sheetmetal work, engine conversion
retro car restoration and tuning
|
|
NS Dev
|
posted on 13/5/06 at 11:11 PM |
|
|
quote: Originally posted by DIY Si
Fancy making me one when I get that far?
Go on, pleeeaaaassseee?
Depends how far away from that point you are!
At the moment I am seriously short of time, as I want my car on the road this summer, but later in the year I will be able to take on some work.
You'd probably have to get the bends though as it might be a bit cheeky for me to buy them from an exhaust manufaturer to make a manifold to
sell on!!
Retro RWD is the way forward...........automotive fabrication, car restoration, sheetmetal work, engine conversion
retro car restoration and tuning
|
|
DIY Si
|
posted on 13/5/06 at 11:13 PM |
|
|
I'm just about to finish making the chassis, and have a de-deon kit on the way, so won't need an exhaust for some time yet. I can get
whatever bits you think you'd need from sdw. They're a 10 min drive from me.
|
|
NigeEss
|
posted on 13/5/06 at 11:16 PM |
|
|
Seriously impressed
Well don Nat.
|
|
omega0684
|
posted on 13/5/06 at 11:27 PM |
|
|
could you do pinto exhaust manifolds?
exhaust is very impressive!
I love Pinto's, even if i did get mine from P&O!
|
|
NS Dev
|
posted on 13/5/06 at 11:31 PM |
|
|
I could in the future, but not for the next couple of months, flat out with 7, racing grasser, spannering for a radical SR3 team, building a new
grasser, going on Run to the sun, rebuilding a Manta and going on holiday to Siberia!! (oh and prob starting a new job as well!)
Retro RWD is the way forward...........automotive fabrication, car restoration, sheetmetal work, engine conversion
retro car restoration and tuning
|
|
Simon
|
posted on 13/5/06 at 11:52 PM |
|
|
quote: Originally posted by andylancaster3000
Thats really quite impressive! Going to have to do the same thing not long from now but was wondering a few things. Is stainless welding much harder
then mig welding? Also, where did you buy the bends from?
Cheers,
Andy
Welding stainless with a tig is an absolute pleasure
I've tigged ally, mild & stainless and bronze (for work (loads)). Only mig'd mild and reckon stainless is second only to bronze for
ease of welding.
Must buy a roll of stainless to try in my mig.
NS - very nice job
ATB
Simon
[Edited on 13/5/06 by Simon]
|
|
NS Dev
|
posted on 14/5/06 at 12:03 AM |
|
|
Simon, when you TIG ally (well, when I tig ally!) how do I stop the filler rod melting due to proximity to the arc, while still keeping it in the gas
between dips!!????
I've been playing but it seems that I keep balling up the end of the filler rod and it gets black scum on it between dips, which buggers up the
weld.
Any pointers??
Retro RWD is the way forward...........automotive fabrication, car restoration, sheetmetal work, engine conversion
retro car restoration and tuning
|
|
Dante
|
posted on 14/5/06 at 04:37 AM |
|
|
quote: Originally posted by NS Dev
I've been playing but it seems that I keep balling up the end of the filler rod and it gets black scum on it between dips, which buggers up the
weld.
Any pointers??
NS, I find that when I'm welding aluminum the process is greatly facilitated by heating up the work a good deal. If there's a better way
of getting good welds I'd love to know it, heating each time is a pain.
What welder did you get?
|
|
big_wasa
|
posted on 14/5/06 at 06:18 AM |
|
|
Nat,
nice work Is it fully welded or just tacked in place ? as its so neat.
Im just about getting the hang of my mig but I love how neat tig is . How hard is it to teach your self to do mild and stainless ? Ive found a course
locall to me for about £250 but that would go a long way towards a good used machine if I could teach my self ??????????????????????
 
|
|
Macbeast
|
posted on 14/5/06 at 06:48 AM |
|
|
Brilliant work Dev. Put me down for a Pinto manifold when you've got time 
|
|
907
|
posted on 14/5/06 at 06:58 AM |
|
|
Hi Nat,
Proud? So you should be. Well done.
It's not just the money you save though,
it's when someone says, "that nice, where did you get that?"
 "I made it"  (smug grin)
What size is yours? (oo err)
With ceramics, big is best. Pic below shows my torches.
On the right is the one that came with my inverter. Little ceramics are great for getting in tight angles.
The ceramic on its own is the biggest I've got.
The torch on the left is the same as I use at work, rescued from the bin, as a lump of hot metal burnt
through it. It's still 3.5M long, plenty for home use.
Argon exits a large ceramic at lower velocity and spreads more. Literally, better gas flow all round.
atb
Paul G
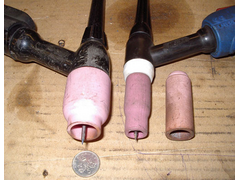 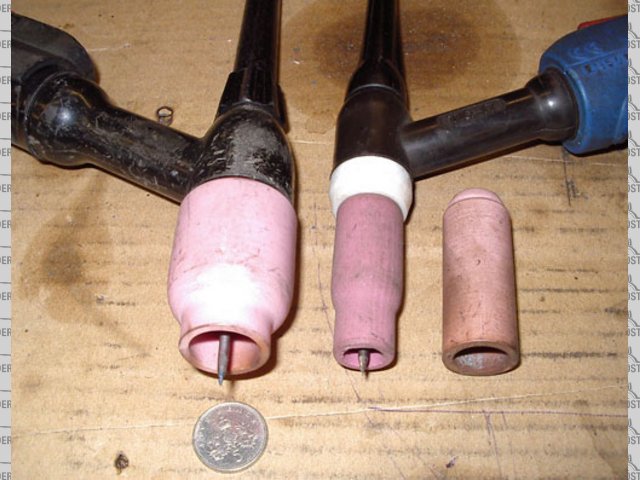 Rescued attachment tig-lens-002s.jpg
|
|
Jon Ison
|
posted on 14/5/06 at 07:13 AM |
|
|
Nat, top job.
Nat, wrong engine........
|
|
nitram38
|
posted on 14/5/06 at 07:36 AM |
|
|
quote: Originally posted by NS Dev
Simon, when you TIG ally (well, when I tig ally!) how do I stop the filler rod melting due to proximity to the arc, while still keeping it in the gas
between dips!!????
I've been playing but it seems that I keep balling up the end of the filler rod and it gets black scum on it between dips, which buggers up the
weld.
Any pointers??
It sounds like you are holding the torch at too steep an angle. Try making the tungsten as close to 90 degrees to the weld pool as poss.
This will ensure a more direct 'arc' and when you intoduce the rod it will only melt in the smaller area. Also the sheilding gas will be
more even and you should not get the blackening you are talking about.
Also make sure that you are using a rounded tungsten that is closer to the ceramic. The photos of the torch in the previous posts are set up to steel
or stainless, because the tungstens are pointed and stick out further than the alloy setup.
[Edited on 14/5/2006 by nitram38]
|
|
Krismc
|
posted on 14/5/06 at 08:15 AM |
|
|
quote: ...Nat, top job.
yea and the rest... i think thats bloody brilliant, i think you should do a how too course in ya garage £25 for a days course 
how about it??
PS i have a doner vehicle
Built, Ivaed, Drove and now Sold - 2011 MNR VORTX RT+ 2000cc Zetec on R1 Throttle boddies.
|
|
mark chandler
|
posted on 14/5/06 at 08:33 AM |
|
|
Really neat and tidy, hours of pleasure doing that.
Please can you let me know the order that you approached the construction, i.e. which parts you made first and the order of assembly ?
Cheers Mark
|
|
ditchlewis
|
posted on 14/5/06 at 09:05 AM |
|
|
wonderful job, just wish i could do that.
you're the man....
ditch  
|
|
NS Dev
|
posted on 14/5/06 at 09:32 AM |
|
|
quote: Originally posted by 907
Hi Nat,
Proud? So you should be. Well done.
It's not just the money you save though,
it's when someone says, "that nice, where did you get that?"
 "I made it"  (smug grin)
What size is yours? (oo err)
With ceramics, big is best. Pic below shows my torches.
On the right is the one that came with my inverter. Little ceramics are great for getting in tight angles.
The ceramic on its own is the biggest I've got.
The torch on the left is the same as I use at work, rescued from the bin, as a lump of hot metal burnt
through it. It's still 3.5M long, plenty for home use.
Argon exits a large ceramic at lower velocity and spreads more. Literally, better gas flow all round.
atb
Paul G
Cheers Paul!
I do use a pretty big ceramic. I bought a load of smaller ones and some 1.6 tungstens but found that I got on much better with 2.5mm tungstens
sharpened to a razor point, with a gas lens and a number 8 gas lens ceramic, that's what I used on all of the manifold.
Only tricky bit was getting between the pipes at the collector, where I just turned the gas right up and extended to tungsten about 1" past the
cup!!!!!
cheers for the advice over the last week or two!!
Retro RWD is the way forward...........automotive fabrication, car restoration, sheetmetal work, engine conversion
retro car restoration and tuning
|
|
NS Dev
|
posted on 14/5/06 at 09:42 AM |
|
|
quote: Originally posted by big_wasa
Nat,
nice work Is it fully welded or just tacked in place ? as its so neat.
Im just about getting the hang of my mig but I love how neat tig is . How hard is it to teach your self to do mild and stainless ? Ive found a course
locall to me for about £250 but that would go a long way towards a good used machine if I could teach my self ??????????????????????
Fully welded of course!!!! Just very small welds so they are tricky to see!
Following my experience I would say you will pick up TIG on steel (mild or stainless, the latter is prob easier cos its usually much cleaner steel)
very quickly, particularly if you can gas weld (but I have never really done much gas welding and I didn't struggle)
Basically it's the same as with mig, go VERY slowly, and watch what IS happening, not what you want to happen. If you get a machine, there a
several people on here who do the job for a living and can offer you great advice, that's where I found out most of my info, plus various free
internet downloads.
It's very satisfying!!
Don't buy a cheap chinese inverter if oyu can avoid it. The GYS inverters are as cheap as any really and are french built and prob the cheap DC
inverter to go for, but obviously you can't weld ally with them. if you want to weld ally consistently and with a reliable machine you either
need a decent used inverter from Lincoln, Miller, Murex and the like, or a used thyristor machine like my ESAB, which are around £750 recon with new
torch etc etc.
Retro RWD is the way forward...........automotive fabrication, car restoration, sheetmetal work, engine conversion
retro car restoration and tuning
|
|