britishtrident
|
posted on 7/1/06 at 01:51 PM |
|
|
quote: Originally posted by Fred W B
Adding these 1.6 mm ally pressed up side boxed panels to the sides of my proto middy chassis increased torsional rigidity from 2700 ft/lb/Deg to 5700
ft/lb/fl/Deg.
Cheers
Fred WB
Much the same as Ron Taurnac did on F1 Brabahams in the late 60s.
The torsional stiffness gain is because the ally sheet material round out side of the structure --- ie considerable distant from the the neutral
axis. However normally I wouldn't expect so big a gain --- I would guess you used relative thick material ?
|
|
|
britishtrident
|
posted on 7/1/06 at 01:55 PM |
|
|
Many production cars including my own R75 use alloy lower wishbones other production cars like the Mondeo use wishbones made of steel pressings
--- the Mondeo wishbone is lighter it weighs next to nothing.
|
|
smart51
|
posted on 7/1/06 at 07:31 PM |
|
|
quote: Originally posted by britishtrident
Many production cars including my own R75 use alloy lower wishbones other production cars like the Mondeo use wishbones made of steel pressings
--- the Mondeo wishbone is lighter it weighs next to nothing.
A cast alloy wishbone with machined mounting faces will be dimensionally more accurate than a two piece welded steel pressing. You have to choose
between accuracy / cost / weight.
I worked on a machine to set up the toe / camber angles for a production axle for a major car company a few years ago. It was welded up from a number
of pressings. Their philosophy seemed to be make it from really cheap and inaccurate stuff and then adjust the eccentric bolts to get the accuracy
spot on. It did seem to work.
|
|
907
|
posted on 8/1/06 at 01:25 AM |
|
|
The Problem with Aluminium is... (IMHO)
When aluminium is manufactured it is cast into large billets.
As it cools and solidifies it forms into crystals that are uniform in shape and size.
Diagram A below is a simplified version of what might be seen under magnification.
In this state it has a tensile strength of 4 to 6 tons/sq inch. (steel is 25 to 30)
Aluminium is however extremely malleable and can be cold formed into usable shapes,
rolled into sheet, drawn through dies, or drawn over mandrels to form hollow sections.
This stretches and compresses the crystal structure as in diagram B.
This has the effect of greatly increasing the tensile strength, depending on the amount. (Work hardening).
Unfortunately, when we then weld this structure, we locally anneal it and in the weld itself
reform the crystals as in diagram A, and consequently back to it's lower tensile strength.
Diagram C shows a welded fabrication similar to areas of a chassis.
The main structure would be strong, but the red areas would be weak.
Under load, either constant, but more so alternating, these areas would be prone to failure.
So it's glue, bond, rivet or bolt.
Welding this type of structure is a no no.
Paul G
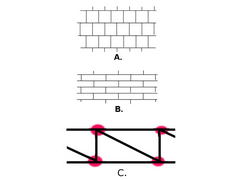  Rescued attachment Al-structure-merge-s.jpg
|
|
britishtrident
|
posted on 8/1/06 at 04:02 PM |
|
|
Nicely put 907
|
|
907
|
posted on 8/1/06 at 05:13 PM |
|
|
quote: Originally posted by britishtrident
Nicely put 907
Thanks.
I just wish I could "do" electrics, spray paint, and take things off engines without loosing the skin off me knuckles.
Paul G
|
|
02GF74
|
posted on 9/1/06 at 09:57 AM |
|
|
quote: Originally posted by cymtriks
Aluminium can be used to make very light structures. But not spaceframes. as has been said above it's a third of the weight but also a third of
the strength in tension or compression so to get the same strength as a steel spaceframe you'd need to triple the amount of metal which gives
you the same weight as a steel chassis only with worse fatigue life and at higher cost. Pointless.
hmmm, I looked up some aluminium alloy data in the past and yes, it is 1/3rd the weight but approx. 1/2 strength in its raw form; there are alloy that
approach steel in strength (the word being used in the vaguest non engineering sense).
|
|
flak monkey
|
posted on 9/1/06 at 10:17 AM |
|
|
Most of the alloys that approach steel in strength do so through solution heat treatment and precipitation hardening. When you weld these alloys they
effective temper and return to the strength of normal ali (within a bit). To get the strength back you need to heat treat the whole chassis once it
has been welded, not easy!
As has been said, ali is ok for some structures, but not for spaceframes.
David
Sera
http://www.motosera.com
|
|