MikeRJ
|
posted on 16/8/06 at 03:35 PM |
|
|
quote: Originally posted by JulianT
The chassis has been periodically crack tested without incident.
How is this done on something as large as a locost chassis? I know you can xray and ultrasonicaly test small parts for cracks.
|
|
|
iank
|
posted on 16/8/06 at 03:50 PM |
|
|
I'd guess Dye Penetrant Crack Testing.
Testing the whole car would be expensive, but doing localised tests in high stress areas (suspension mounts etc) would be managable.
|
|
macintosh
|
posted on 16/8/06 at 09:22 PM |
|
|
quote: Originally posted by andyps
Have a look in the running gear section for plans from Rorty for both IRS and DeDion to fit the standard chassis and Sierra running gear
Actually Racetech (and Lada) is in my region, (180 km from here :-) )and it is suitable donor for book chassis. Have to admit, Lada is crap from point
of quality, but he same time its really, really, rally cheep and there is tons of spare parts around for free or allmost for free.
And I think lada uprights are very usable (as i recall they are forged and reliable), at least Racetch uses lada uprights.
And what i have heard - lada engine is very tunable (i think Formula Estonia used them - best Formula Cars in eastern block before glasnost)
More info about Eastern Block racing cars:
http://www.autosoviet.altervista.org/ENGLISH-automotorusse-formula.htm
http://recce.pri.ee/album29/fotod.html
|
|
kb58
|
posted on 17/8/06 at 12:43 AM |
|
|
I'm glad it has been reliable. Apparently the engineers calculated the proper material thickness to prevent cracking - so far. But one chassis
lasting five years doesn't mean an aluminum chassis is an easy, no-brainer, to be built same as a steel one.
Based upon what I've read, I will never make an aluminum chassis. I wonder what the torsional stiffness is of that one. Regardless, it's
not an issue about *if* it will crack, but when, because it will. Hopefully it will be after you've sold it, so make sure any future buyer is
aware.
There is a very good reason aluminum aircraft fuselages are removed from service at some point - the engineers knowing when it has become unsafe.
Porsche experimented with aluminum race car chassis, and gave up on them. These two groups know what they're doing, and we don't...
quote: Originally posted by JulianT
Hi
I'm the proud owner of a Locost7 Fireblade with an aluminium chassis.
The chassis has been rock solid for the last 5 years without any signs of cracking.
When I built it I had everyone and their mother saying it would not work....it will crack (it has not), it will bend(no), it will be hard to make(it
was easy)...you get the picture.
The chassis has been periodically crack tested without incident.
Julian
Mid-engine Locost - http://www.midlana.com
And the book - http://www.lulu.com/shop/kurt-bilinski/midlana/paperback/product-21330662.html
Kimini - a tube-frame, carbon shell, Honda Prelude VTEC mid-engine Mini: http://www.kimini.com
And its book -
http://www.lulu.com/shop/kurt-bilinski/kimini-how-to-design-and-build-a-mid-engine-sports-car-from-scratch/paperback/product-4858803.html
|
|
JulianT
|
posted on 17/8/06 at 09:55 AM |
|
|
Dear KB58
I'm an aircraft engineer by trade, working on commercial and military transports. Every aircraft, irrespective of construction has a series of
inspection or service points in it’s life. These points are based on flight hours, landings or specific incidents (perhaps a heavy landing). As each
point is reached different inspections are required. An aircraft can go on indefinitely as long as the rules are followed, it’s generally certain
components or locations that are very carefully checked and if required replaced. As an example hundreds perhaps thousands of WW2 aircraft are still
happily flying. Currently I’m working on an aircraft called a Nimrod, it’s basically a 1950’s Comet airliner that had been modified as an anti
submarine aircraft, it has been in UK military service ever since. We are rebuilding it for about the fourth time.
I’m certainly not going to recommend that aluminium is the way to go, I’m not even going to recommend it to anyone, it is however quite possible if
you know what you are doing. You are very right to say people should not try it. My point is that I’m constantly amazed by the half truths presented
as fact on this subject, every material has it’s ups and downs. My car and a dozen others I know about show it can be done – as long as you know the
rules.
If you want to see something really scary, just go to a kit car show and walk round the public car park and look at the welding on some of the home
made steel chassis.
I’ve had the welding X-ray’d a couple of times after construction and used an ultraviolet process since. A local aviation college is very happy to do
it for free, they use it as a training exercise for students.
All the best Julian
|
|
Liam
|
posted on 17/8/06 at 12:29 PM |
|
|
Car looks very nice indeed, and welcome to the forum...
Out of interest what grade of ally have you used and what wall thickness is it? Do you know what it weighs and how stiff it is? Sure you can
overcome the disadvantages of using this relatively 'difficult' material with the right knowledge, careful fabrication and constant
rigorous checking, but have you actually gained any advantage with an ally copy of the book locost not-particularly-good-steel-spaceframe to make it
worthwhile?
Liam
[Edited on 17/8/06 by Liam]
|
|
kb58
|
posted on 17/8/06 at 08:48 PM |
|
|
quote: Originally posted by JulianT
it is however quite possible if you know what you are doing. You are very right to say people should not try it. My point is that I’m constantly
amazed by the half truths presented as fact on this subject, every material has it’s ups and downs. My car and a dozen others I know about show it can
be done – as long as you know the rules.
Julian
That is exactly the problem, we don't know what we are doing, at least from a strength-of-materials and material fatigue point of view.
I'm not saying don't use it because it won't work, but that we don't know how to use the material correctly.
Regarding the aluminum chassis in question, does anyone know what the torsional strength is? Or what it is compared to a steel equivalent? What does
it weigh?
I guess I'm assuming that we amateur builders (myself included) don't in fact know the rules... forgive me for those of us who do.
Mid-engine Locost - http://www.midlana.com
And the book - http://www.lulu.com/shop/kurt-bilinski/midlana/paperback/product-21330662.html
Kimini - a tube-frame, carbon shell, Honda Prelude VTEC mid-engine Mini: http://www.kimini.com
And its book -
http://www.lulu.com/shop/kurt-bilinski/kimini-how-to-design-and-build-a-mid-engine-sports-car-from-scratch/paperback/product-4858803.html
|
|
KENLUDE97
|
posted on 17/8/06 at 11:14 PM |
|
|
KB i can get most of that for you in the morning. Other than how long it will last.
|
|
Fred W B
|
posted on 18/8/06 at 05:52 AM |
|
|
To compare the mass of steel to ally, multiply steel thickness by 8.07 to get a factor, and the ally by 2.73.
so 1.6 x 8.07 = 12.9
12.9 / 2.73 = 4.72.
so for the same mass you can use 4.7 mm ally or 1.6 steel
The mass of a block of steel would be L (in metre) x W (in metre) x thickness (in millimetre) x 8.07 = KG
Cheers
Fred W B
[Edited on 18/8/06 by Fred W B]
|
|
KENLUDE97
|
posted on 18/8/06 at 01:28 PM |
|
|
JulianT how much does your car weigh? its got to be LIGHT! Nice looking car too!
Steel is stronger than aluminum.
Aluminum is stiffer than steel.
Steel is more elastic than aluminum.
Aluminum boesn't bend it snaps and generally at the weld.
I did some rough weight caculations for steel and aluminum chassis.
STEEL - 1"sq x .06wall x 12"lg = .76lb/ft x 120' = 91lb (41kg) frame
STEEL - 1.25"sq x .06wall x 12"lg = .97 lb/ft x 120' = 116lb (53kg) frame
ALUMINUM - 1"sq x .06wall x 12"lg = .26lb/ft = 31lb (14kg) frame
ALUMINUM - 1"sq x .13wall x 12"lg = .53lb/ft x 120' = 64lb (29kg frame
ALUMINUM - 1.25"sq x .06wall x 12"lg = .33lb/ft x 120' = 40lb (18kg) frame
ALUMINUM - 1.5"sq x .10wall x 12"lg = .66lb/ft x 120' = 79lb (36kg) frame
[Edited on 8/18/06 by KENLUDE97]
|
|
NS Dev
|
posted on 18/8/06 at 01:58 PM |
|
|
ahh the good ol' ally frame discussion again!
Funny when this keeps coming around, and everybody divides into the "it'll snap in half" and the "its really cool and
light" camps!!
At some point somebody will realise that building a "locost" chassis from welded ally box is like building a cathedral from expanded
poystyrene or inventing a titanium steam powered beam engine................................
Use the technology to its advantage, don't apply it to a design not meant for that material.
This is one occasion where I will mention Robin Hood cars without criticising too much, as their "cheesegrater" was actually an attempt to
use ally properly in a "7 type vehicle"
I suggest a good look at the construction techniques used in the Lotus Elise and the monocoque Lolas would be a good starting point.
For a starter for ten......there aint any welds!
Retro RWD is the way forward...........automotive fabrication, car restoration, sheetmetal work, engine conversion
retro car restoration and tuning
|
|
kb58
|
posted on 18/8/06 at 03:22 PM |
|
|
quote: Originally posted by JulianT
Dear KB58
Currently I’m working on an aircraft called a Nimrod, it’s basically a 1950’s Comet airliner
Wasn't the Comet the aircraft where several crashed and the cause traced to not understanding metal fatigue? As I recall it was the pressure
cycling as the aircraft climbed to altitude and down again. They finally found it by filling a fuselage with water(!) and cycled the pressure. The
lead engineer was called late one night, "I think you better come look at this." The fuselase had indeed split. It marked the death of
British airliners because by then the US builders had watched and learned what had happened, then come out with thier own fleet.
Anyway, the irony here is that we're discussing metal fatique and you brought up the one aircraft that made metal fatique famous.
[Edited on 8/18/06 by kb58]
Mid-engine Locost - http://www.midlana.com
And the book - http://www.lulu.com/shop/kurt-bilinski/midlana/paperback/product-21330662.html
Kimini - a tube-frame, carbon shell, Honda Prelude VTEC mid-engine Mini: http://www.kimini.com
And its book -
http://www.lulu.com/shop/kurt-bilinski/kimini-how-to-design-and-build-a-mid-engine-sports-car-from-scratch/paperback/product-4858803.html
|
|
marc n
|
posted on 19/8/06 at 07:41 AM |
|
|
we once had a f27 alloy chassis at our workshop, made from 40mm od x 2.5 wall durol with 4mm gusset plates etc, the problem was that the size of the
tubing meant two things
1. the cockpit space was tiny im only 8 1/2 stone and 5 foot 9 and i could barley fit in
2. it was 20 kilos heavyier than a fully triangulated steel chassis with full t45 cage ( did look impressive though ) apparantley they only made three
due to costs and the fact is was heavier than the the steel spaceframe.
please email rather than u2u
direct workshop email ( manned 8am till 6pm )
www.mnrltd.co.uk enquireys to :-
chrismnrltd@btinternet.com
|
NOTE:This user is registered as a LocostBuilders trader and may offer commercial services to other users
|
Peteff
|
posted on 19/8/06 at 05:50 PM |
|
|
im only 8 1/2 stone and 5 foot 9
How old are you ? 12. . How much does aluminium tube cost compared to steel of a comparable strength and can you weld it with a £200 mig running
cheap co2 cylinders? That is the only consideration for a Locost in my estimation. If it's going to cost more to buy and more to build
it's defeating the object of the excercise. edit:-
Just a question for you Julian, how many miles has it done in the 5 years on the road? It's not done many in the picture from the rust on the
disks.
[Edited on 19/8/06 by Peteff]
yours, Pete
I went into the RSPCA office the other day. It was so small you could hardly swing a cat in there.
|
|
marc n
|
posted on 19/8/06 at 06:13 PM |
|
|
quote:
How old are you ? 12. .
 been same weight and height since i was 14 ( it must be the smoking )
please email rather than u2u
direct workshop email ( manned 8am till 6pm )
www.mnrltd.co.uk enquireys to :-
chrismnrltd@btinternet.com
|
NOTE:This user is registered as a LocostBuilders trader and may offer commercial services to other users
|
DIY Si
|
posted on 19/8/06 at 06:25 PM |
|
|
Same here, except same since I was 15 and it's been 6'3" and 14 1/2 stone! Plenty of space in my car!
“Let your plans be dark and as impenetratable as night, and when you move, fall like a thunderbolt.”
Sun Tzu, The Art of War
My new blog: http://spritecave.blogspot.co.uk/
|
|
NS Dev
|
posted on 20/8/06 at 09:54 AM |
|
|
quote: Originally posted by kb58
quote: Originally posted by JulianT
Dear KB58
Currently I’m working on an aircraft called a Nimrod, it’s basically a 1950’s Comet airliner
Wasn't the Comet the aircraft where several crashed and the cause traced to not understanding metal fatigue? As I recall it was the pressure
cycling as the aircraft climbed to altitude and down again. They finally found it by filling a fuselage with water(!) and cycled the pressure. The
lead engineer was called late one night, "I think you better come look at this." The fuselase had indeed split. It marked the death of
British airliners because by then the US builders had watched and learned what had happened, then come out with thier own fleet.
Anyway, the irony here is that we're discussing metal fatique and you brought up the one aircraft that made metal fatique famous.
[Edited on 8/18/06 by kb58]
Being picky, wasn't quite the death of british airliners, there was the trident which was a outstanding plane as far as I know (but I'm no
expert)
It certainly put most of the nails in the coffin though!!
Retro RWD is the way forward...........automotive fabrication, car restoration, sheetmetal work, engine conversion
retro car restoration and tuning
|
|
kb58
|
posted on 20/8/06 at 06:55 PM |
|
|
Thanks, yeah I almost didn't post that, afraid it would start some defensive "lively" discussion.
Since we are discussing aluminum metal fatigue though, it's sadly a perfect example of the consequences of using aluminum without knowing the
qualities of the material. And most of us don't either, myself included...
[Edited on 8/21/06 by kb58]
Mid-engine Locost - http://www.midlana.com
And the book - http://www.lulu.com/shop/kurt-bilinski/midlana/paperback/product-21330662.html
Kimini - a tube-frame, carbon shell, Honda Prelude VTEC mid-engine Mini: http://www.kimini.com
And its book -
http://www.lulu.com/shop/kurt-bilinski/kimini-how-to-design-and-build-a-mid-engine-sports-car-from-scratch/paperback/product-4858803.html
|
|
JulianT
|
posted on 22/8/06 at 11:12 AM |
|
|
The chassis is made of an Ali alloy - 7075, it has zinc and copper added. The welding was not done by me. The tubes were pri heated in a oven before
welding.
The tubes were left over from an MOD project so cost nothing (in true Locost fashon). The car weighs 350kgs and has done 3800 miles. Standard 120hp
893cc Fireblade.
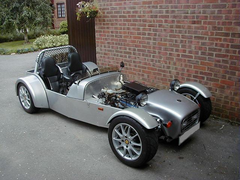 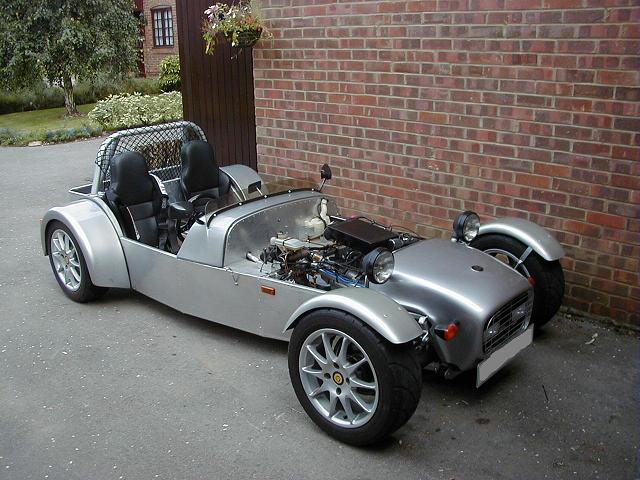 Rescued attachment I~0000772.JPG
|
|
ChrisGamlin
|
posted on 27/8/06 at 04:05 PM |
|
|
Hi Julian
This brings back memories, I think it was yourself who invited me over for a nose around your car about 5 years ago before I started building
mine!!
I must say Ive always been slightly concerned with the straight transfer of design from steel to alu, but glad to see it has survived and is still
going strong. IIRC this was the alu chassis built by Ron Champion wasnt it, with thicker wall tube than a steel equivalent chassis? Sorry if
I've sistaken you for someone else, but Im sure it was around the Newbury area and it was definitely a silver alu chassis'd Locost, so
there can't be too many of you!
All the best
Chris
[Edited on 27/8/06 by ChrisGamlin]
|
|