02GF74
|
posted on 5/6/06 at 02:46 PM |
|
|
thanks to y'all (especailly Darren) for pointing this one out - need to have a look at my ones
From memory the lower ball joint is transit - do I need to get a threaded tube and weld it inside the lower tube or is there some other (simpler but
not necessarily cheaper) solution?
|
|
|
DarrenW
|
posted on 5/6/06 at 03:12 PM |
|
|
iirc my lower bone uses the ball joint from a Maxi which is bolted onto a plate - ie doesnt use the threaded insert / nut. Ive no idea how you'd
convert a F27 bone to do that though ref geometry etc.
|
|
pewe
|
posted on 5/6/06 at 03:24 PM |
|
|
F27 owners club reckon only 2 like this in 12 years - but doesn't help those 2 owners. I reckon I'll put a strap top and bottom of the nut
sides and rosette weld there and then back onto the wishbone tube. Current F27 marque owner Peter Allan of Image Sports Cars reckons they have
re-desingned the bottom wisbone so it sandwiches the ball joint pick-up tube. Cheers, Pewe 
|
|
02GF74
|
posted on 5/6/06 at 03:31 PM |
|
|
quote: Originally posted by pewe
F27 owners club reckon only 2 like this in 12 years
bear in mind that is 2 owners that lived to tale the tail; not sure how information about those that didn't would get publicised......
|
|
MikeRJ
|
posted on 5/6/06 at 03:42 PM |
|
|
If it uses the transit drag link (as per locost top wishbone), then it shouldn't be too difficult to rebuild the wishbones using the threaded
tube available from Lolocost and probably many of the other Locost suppliers.
|
|
pewe
|
posted on 5/6/06 at 03:44 PM |
|
|
yep, you're right that's why I'm going for a belt & braces fix. Cheers, Pewe
|
|
gregf27
|
posted on 5/6/06 at 10:28 PM |
|
|
I'm glad that my mishap has raised awareness!!
bit worried that my attempt to strengthen it was poo pood!!,
before I put it back on the road I want to make sure its 100% safe - I drive my little boy round in it mostly.
I have got hold of a newer set of wishbones , that have the threaded insert welded in,
Do you think this will be ok?, or should I put a strengthening bar accross the two arms, to make a bit of a triangle?,
Your comments please!!
Greg
[img][/img]
|
|
Liam
|
posted on 5/6/06 at 10:49 PM |
|
|
That looks a hell of a lot better!
By a bar accross the two arms to form a triangle, do you mean right near the bushes? No point at all as far as i'm concerned. The chassis does
that job for you. I've seen that caterhams have a very thin tube on there wishbones in this location, and the only possible reason for it that
i can see is to stop the wishbone pulling in during welding. In fact I wish i was aware of this when I made my bones! As it is, that's an
elegant and pure wishbone - no bits of plate causing stress concentrations, nothing applying bending loads, and the minimum possible welding.
I'd say leave it like that, it should be fine.
Liam
[Edited on 5/6/06 by Liam]
|
|
Avoneer
|
posted on 5/6/06 at 10:49 PM |
|
|
I'd be tempted to put a 6mm plate gusset with a curved edge in there welded to the inside edges of each arm (not top or bottom)
Crap pic I know, but you should get the idea.
Pat...
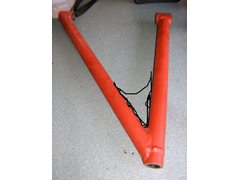  Rescued attachment 1.jpg
No trees were killed in the sending of this message.
However a large number of electrons were terribly inconvenienced.
|
|
Liam
|
posted on 5/6/06 at 11:03 PM |
|
|
Wouldn't bother with that myself. If you're mounting a shock or plate mounted ball joint then yeah, but otherwise it wont help.
It's already an ideal structure with straight members directly linking the nodes. A plate will just apply stress concentration and bending to
the tubes where it ends, and the welding wont do any good either. All imho of course.
Liam
|
|
nitram38
|
posted on 5/6/06 at 11:38 PM |
|
|
Compared to my car, your bones are much shorter than mine.
Because mine is a single seater design, the body is the width of one person, so my bones are very long.
My triangulation is because of this. On short bones, I would not bother with triangulation, but it would not cause any harm to do so.
Looking at the bush though, is it just a butted seam weld around the end of the bush or does the bush extend further into the tube?
If it is just a butt weld, it is much better than the originals, but I would have made a longer bush and cut half of the tube away and then welded
the bush in.
This would create two half moon welds (which equal your butt weld) but also two logitudinal welds that run the length of the bush.
This would create two different opposing shears and this will make the joint stronger.
Take a look at my earlier photo.
[Edited on 5/6/2006 by nitram38]
|
|
907
|
posted on 6/6/06 at 12:09 AM |
|
|
Hi All
It looks to me as if part of the weld has been broken for some time.
The silver areas are newly fractured metal.
The brown areas, arrowed, are old cracks. (IMHO)
I would like to know what grade of nut this is.
Possibly a high tensile, higher carbon content? This could explain the fracture.
Paul G
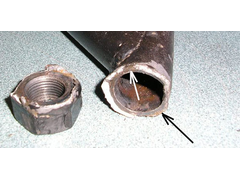  Rescued attachment wishbone2smls.jpg
|
|
MikeRJ
|
posted on 6/6/06 at 12:31 AM |
|
|
quote: Originally posted by Liam
Wouldn't bother with that myself. I
Me either, the newer bones look infinitely better designed. No need for any gussets etc. IMO.
|
|
JB
|
posted on 6/6/06 at 04:56 AM |
|
|
Gusset
If you do want to put a gusset in then it would be better on the top or bottom as the weld is then is shear.
But as mentioned previously the structure would not then be a perfect triangle and put in bending loads.
A wrap around finger plate would be a good idea. I know the picture shows the other end of a wishbone but it is the best picture I could find!
Please note this picture was taken during construction and is a mock up for build purposes.
If you want to see some top class wishbones try to get to a British round of the hillclimb championship and check out a Gould. You will not find
anything on these cars that is not structurally well designed.
John
|
|
pewe
|
posted on 6/6/06 at 08:29 AM |
|
|
Steve Porter who owned F27 reckons that factory cars built within the last 8/9 years have threaded inserts. Also mine are triangulated near the
chassis pick-ups by 12mm diam tube - if it's good enough for Caterham it's good enough for me and I don't believe they put their
brace there to facilitate welding.
Chers, Pewe
|
|
iank
|
posted on 6/6/06 at 09:13 AM |
|
|
quote: Originally posted by pewe
...
Also mine are triangulated near the chassis pick-ups by 12mm diam tube - if it's good enough for Caterham it's good enough for me and I
don't believe they put their brace there to facilitate welding.
Chers, Pewe
I'd guess a brace at the chassis pickups is an attempt to reduce fatigue failures. A wishbone made from two arms without it will try to splay
slightly as the wheel is pushed towards the car. Since there are relatively soft bushes between the wishbone and the solid chassis brackets there
will be a very small bending force at the welded joint allowed as it isn't a perfectly rigid triangle. If there is any kind of crack or
weakness at the welded join it will eventually fail.
|
|
britishtrident
|
posted on 6/6/06 at 12:42 PM |
|
|
More likely it is just to keep the distance between the wishbones eys in spec durring manufacture and storage.
|
|
Nisseven
|
posted on 7/6/06 at 11:02 AM |
|
|
That 12mm brace has been recomended to me by a person I have great respect for as an engineer. As has already been mentioned it stops the slight
splaying on the wishbone onder loading due to the compliance of the bushes.
Also IMHO even that new wishbone is pretty ugly for something produced commercially. The mig welding is not pretty and at least it should have been
tigged.
Bruce
|
|