craig1410
|
posted on 4/5/04 at 10:25 PM |
|
|
Yeah, does that mean it will snap instead of just bending? That could be seriously scary!
Interested to learn more though so don't mistake my comment for cynicism...
Cheers,
Craig.
|
|
|
Terrapin_racing
|
posted on 5/5/04 at 11:00 AM |
|
|
Well, the F1 teams have used it and now a number of the university teams competing in Formula Student are doing so also. No failures reported.
Car 12
May 1st 2002
Car 12 marks the fifth generation of UBRacing car and is based strongly on evolution not revolution. The team is made up of 14 Mechanical Engineers in
their final year of BEng and MEng courses. The small team was divided into four design groups, Engine, Suspension, Chassis and driver environment and
Drive train. These design groups along with regular whole team meetings have enabled the team to produce the most integrated and well-developed car to
date.
The design philosophy was centred around the use of CATIA for the purpose of design integration, design analysis and parts management. The main
vehicle concepts that have been designed in from day one are, reliability, innovation, manufacturability, driveability and easy of maintenance and of
course performance.
Key design features include in house magnesium cast wheels, an evolution of the rear load transfer device first seen on last year's UBRacing
car, integrated uprights and callipers and MMC brake disk with a Keronite coating. The drivetrain has also received considerable attention with an
in-house miniaturised differential housing and lightweight CV housings. Engine developments include a vortex induction plenum, rapid prototype
injector housings and a carbon fibre restrictor.
The team completed their goal of early car completion, with the car being launched on the 20th of March. The early launch was achieved due to the
team's philosophy of design for manufacture, extensive use of in-house facilities and manufacturing planning. This has given the team sufficient
time to fully test and develop the car.
The team feels that as a consequence of its integrated design approach, extensive use of CATIA for the purpose of drafting and finite element analysis
and design for manufacture philosophy, a car has been produced that has both very high performance, but is innovative and reliable.
Chassis
- Lightweight T45 / mild steel space frame
- Aluminium bonded and fully stressed honeycomb floor
Engine
- Honda CBR600 FX
- Fuel injection with MBE custom mapped engine management system
- Power @ 12000rpm 80 bhp
- Torque @ 8500rpm 61 lb/ft
- Modified valve timing
- Suzuki GSXR750 injectors
- 35mm throttle body for increased throttle response
- Tuned aluminium intake for maximum torque at 10000rpm
- 4-2-1 stainless steel exhaust tuned for top end power
- Hydroflow quick release coolant system
- Electric water pump supplying more efficient and reliable cooling
- Dual pass high density core radiator with high laminar flow ducting
Drivetrain
- In house differential
- In-house cv housings
- 520VM chain driven final drive with ratios from 3.0:1 to 4.0:1
Suspension
- Unequal length non-parallel double wishbones
- In-plane pull rod front push rod rear
- Front anti roll bar
- Rear load transfer device
- Fully adjustable camber, castor and squat
- 2 way adjustable Risse racing shocks
- Stiction reduction by incorporation of bearings throughout system
- Lightened aluminium rockers and uprights
- Nitrotec Treated wishbones
Steering
- Bepsoke in-hose rack
- 150% Ackerman
- 5.5m turning circle
- 270 degree lock to lock steering wheel movement
Brakes
- MMC plasma coated disks
- AP racing 2-pot rear calliper
- Front callipers integrated into front uprights
- Dual circuit with cockpit adjustable bias control
Pedal box and Gear Shift
- Two Pedal tubular Steel Construction
- Quick release with adjustable reach
- Shifter Single action Clutch and gear shift mechanism
- Full throttle gear changes
Additional
- Wheels 13 x 6 In-house magnesium wheels Houssier tyres
- Body 3-piece fibreglass aerodynamically modelled stylish shell
- Quick release fasteners for easy access requiring one person only
- Electrical Completely insulated boxed system, completely weather proof
- Labelled loom and map with easy upgrade options
- Pi Research used for testing and car setup

|
|
Terrapin_racing
|
posted on 5/5/04 at 11:05 AM |
|
|
Oh...and also ...
The amazing new process is Nitrotec. The process can increase the physical properties of the material considerably. The result is a wear surface that
is extremely tough and betters the frictional and corrosion properties of many chrome plating processes with NO chance of hydrogen embrittlement.
[Edited on 5/5/04 by Terrapin_racing]
|
|
crbrlfrost
|
posted on 6/5/04 at 04:01 PM |
|
|
I was curious if you have done any hardness testing, know the thickness of the hardened surface or done any tensile stress to failure testing.
I've looked at the site, and don't really question the information they supply, my question is the information they don't supply.
They don't have any material properties data. F1 gets away with a lot due to lifing of components and data logging <driver go curb hopping
off camera?>. We could life components, but I don't think many of us want to. However, I'm be very interested t hear your results if
you want to keep us posted, and good luck with the season.
|
|
cymtriks
|
posted on 6/5/04 at 09:31 PM |
|
|
So to summarise a long and interesting thread-
If you copy the book design use a bigger tube to compensate for the design shortcommings.
If you want a good design in the first place lean towards the Caterham design with tubes converging on the centre of the lower ball joint and the
spring mounted as close as possible to it.
I have had a quick look at a Caterham in the carpark. I reckon the distance from the ball joint centre to the spring mount centre is just under 2
inches. On the Lowcost it seams to be 4.2 inches. This offset creates a bending moment in the tubes. So the Lowcost wishbone has more than double the
bending forces on a Caterham wishbone.
Does anyone know what kind of ball joint is used on a Caterham wishbone and how it is fixed in place?
|
|
Alan B
|
posted on 6/5/04 at 11:12 PM |
|
|
Mr Cym.....just curious why do you always call locosts "lowcosts"?
Not some freudian disrepect to the beloved Mr Champion by any chance?

|
|
MikeRJ
|
posted on 7/5/04 at 07:50 AM |
|
|
Everything I have read here suggests that wishbones made to book design but with oval tubing should be avoided. Fair comment?
[Edited on 7/5/04 by MikeRJ]
|
|
James
|
posted on 7/5/04 at 08:21 AM |
|
|
quote: Originally posted by MikeRJ
Everything I have read here suggests that wishbones made to book design but with oval tubing should be avoided. Fair comment?
I don't think so at all- bear in mind MK's wishbones are also oval- as are several other manufacturers.
Other than the example shown above (which started this thread), in 2/3 years of reading this site I don't recall anyone saying their wishbones
had bent!
Cheers,
James
[Edited on 10/5/04 by James]
|
|
MikeRJ
|
posted on 7/5/04 at 09:05 AM |
|
|
If the stock design is marginal with tubular steel, then surely oval is only going to make it weaker in bending?
|
|
Terrapin_racing
|
posted on 7/5/04 at 02:18 PM |
|
|
Regarding testing of Nitotec'd wishbones. I was lazy here. I am a judge at FSE and got some test results from the universities whilst at
Bruntingthorpe last year. Their materials and results would have been fine for the Terrapin
However, my material far exceed their spec on diameter and wall thickness etc.
I'll let you know if any break
PS: Can any of you american buds help me- see wanted section 
|
|
jcduroc
|
posted on 7/5/04 at 02:39 PM |
|
|
quote: Originally posted by cymtriks
If you want a good design in the first place lean towards the Caterham design with tubes converging on the centre of the lower ball joint and the
spring mounted as close as possible to it.
I have had a quick look at a Caterham in the carpark. I reckon the distance from the ball joint centre to the spring mount centre is just under 2
inches. On the Lowcost it seams to be 4.2 inches. This offset creates a bending moment in the tubes. So the Lowcost wishbone has more than double the
bending forces on a Caterham wishbone.
Like these, pe (?)
quote: Originally posted by cymtriks
Does anyone know what kind of ball joint is used on a Caterham wishbone and how it is fixed in place?
I'd guess it is still a trunion!... (see pic 2)
Joćo
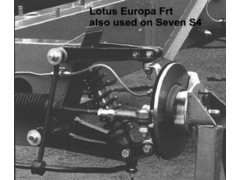  Rescued attachment EuropaFrtSm.jpg
JCM
|
|
jcduroc
|
posted on 7/5/04 at 02:47 PM |
|
|
quote: Originally posted by jcduroc
Like these, pe (?)
HOW DO WE ATTACH TWO PICS IN THE SAME POST???
Joćo
 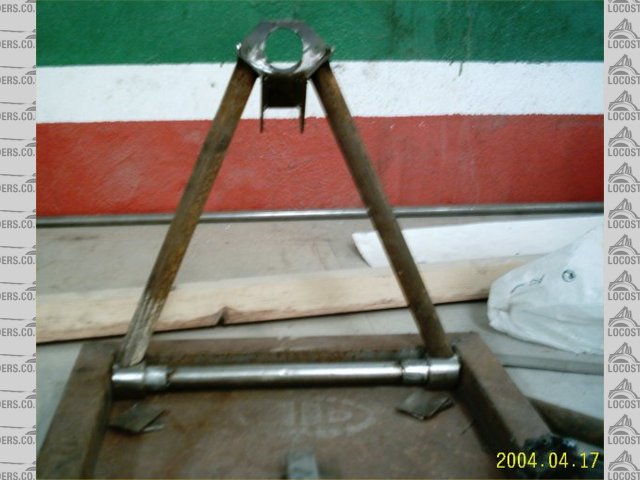 Rescued attachment Img_0070small.jpg
JCM
|
|
dozracing
|
posted on 7/5/04 at 07:23 PM |
|
|
Is this possibly the craziest and pointless thread ever posted on this forum?
Like James said the proof of the pudding is in the eating, and in all the years that cars have been made in this style with oval tubes why has there
never been mention of actual problems encountered with them?
I didn't get my mechanical engineering degree, or my job with the most influencial F1 designer of the past 20 years or my reputation for quality
locost parts because i'm an idiot.
I'm a professional engineer with an approriate background and experience, so i'm hardly likely to supply oval tube wishbones just for the
sake of it if there was a fundamental flaw and that they were likely to have problems.
Its nice of you all to mention my companies name as it must mean its at the front of your minds, but please understand that misleading comments saying
that they should be avoided like the plague does me and the whole locost community no favours at all.
Can we please stick to facts here and not dream up ridiculous statements that have no factual base at all.
Kind regards,
Darren
|
PLEASE NOTE: This user is a trader who has not signed up for the LocostBuilders registration scheme. If this post is advertising a commercial product or service, please report it by clicking here.
|
Jon Ison
|
posted on 7/5/04 at 07:32 PM |
|
|
spot on i seem to remember the little disscussion about my "oval" wishbones been too strong, thus the chassis got wrote off..........
Remember ??
|
|
MikeRJ
|
posted on 7/5/04 at 08:10 PM |
|
|
Darren,
I apologise for my comments. I certainly shouldn't have mentioned your company in that context, it was thoughtless of me. However, I had just
been looking at your web site with a view to purchasing your De Dion conversion, so as you say your company was at the front of my mind. I have
edited my post accordingly.
However, I don't consider this thread crazy or pointless. No-one builds a locost in order to drive an inherently "safe" car around,
but wishbone failure could easily lead to a fatal accident either on road or track. I certainly would like to be fully confident that this
isn't going to happen.
Despite the lack of other reported incidents it has been suggested that the book wishbones are of marginal design. Although I understand the
reasoning behind this, I am not a mechanical engineer and obviously I am not qualified to confirm or deny these suggestions.
Could you extend us the benefit of your experience as to wether you feel the book design (including book materials) is marginal and any possible
failure mechanisms for the two sets of wishbones shown in this thread that have been missed?
|
|
britishtrident
|
posted on 7/5/04 at 08:46 PM |
|
|
Perhaps time to close this thread ?
Going in to Fred Dinah mode -- Nowt wrong with oval tubes provided the size and thickness is adequate--- as I said earlier the thread both both GTS
and MK wishbones are models of good designs unlike the book "thing".
The wishbone in the original picture was a bad interpretation of the book design with poor attention to the details of the shape and postioning of
the mounting plate. The book design causes large bending moments in the wishbone it is so marginal that poor attention to the details of the shape and
position of the mounting plate will push it over the edge especially if the quality and finish of he welding is rough.
Also as I said earlier in the thread Tiger have had to modify the design of wishbone they used because of customers experiencing failures.
The major problem with the wishbone in the picture was a stress raising feature, only mechanical engineers tend to appreciate the importance of
avoiding sharp changes in section. A sharp 90 degree corner is generally taken to increase the local stress by a factor of 3. On the wishbone that
failed under what ever combination of loads occured the increase in stress was enough to initiate local buckling and resulting in buckling of the
whole tube.
|
|
craig1410
|
posted on 7/5/04 at 08:59 PM |
|
|
BritishTrident,
Can you give me your honest opinion on these if you don't mind. I bought these from Lolocost over a year ago (this is an old picture taken just
after I bought them) and they are made from 22mm o/d 2.64mm wall ERW tubing with 3mm thick plate and as you can see the Cortina ball joint.
The welding seems to have very good penetration all round but I am concerned that maybe the top plate has too abrupt an edge where it might tend to
bend like the one at the beginning of this thread. Should I be worried enough to take to it with an angle grinder?
Cheers,
Craig.

|
|
britishtrident
|
posted on 7/5/04 at 09:15 PM |
|
|
quote: Originally posted by craig1410
BritishTrident,
Can you give me your honest opinion on these if you don't mind. I bought these from Lolocost over a year ago (this is an old picture taken just
after I bought them) and they are made from 22mm o/d 2.64mm wall ERW tubing with 3mm thick plate and as you can see the Cortina ball joint.
The welding seems to have very good penetration all round but I am concerned that maybe the top plate has too abrupt an edge where it might tend to
bend like the one at the beginning of this thread. Should I be worried enough to take to it with an angle grinder?
Cheers,
Craig.
The welding is first class and the tube thickness should be sufficent, I had bought them I would be quite pleased but tempted to chamfer the ends of
the plate -- I would probably use some less agressive than an angle grinder.
|
|
MikeRJ
|
posted on 7/5/04 at 09:18 PM |
|
|
quote: Originally posted by britishtridentThe major problem with the wishbone in the picture was a stress raising feature, only mechanical
engineers tend to appreciate the importance of avoiding sharp changes in section. A sharp 90 degree corner is generally taken to increase the local
stress by a factor of 3. On the wishbone that failed under what ever combination of loads occured the increase in stress was enough to initiate
local buckling and resulting in buckling of the whole tube.
I understand this completetly. However, one thing that bothers me which you can probably clear up.
Both wishbones we saw failed by bending in a horizontal plane i.e. the tube bent towards the ground in the middle. In this plane, wouldn't the
reinforcing plate have only a very minor effect on stiffness as it is so much thinner than the wishbone tubing? (i.e. plate offers very little
resistance to bending accross the flat sides).
If the failure had been in the opposite plane, I could quite see how this would be a point of very high stress.
|
|
dozracing
|
posted on 7/5/04 at 10:37 PM |
|
|
Looking at the original picture its hard to give an accurate reason why its bent. But, my i would want to look at the angle its bent at, because the
picture looks as though the tube has bent forward (or backward) and upward.
When we design a wishbone on a Grand Prix car, we first analyse all the loads and we get a worst case loading for each leg of the wishbone, for each
load case.
It maybe of some surprise, but, actually the highest leg loads come from braking on the front and from braking or accelerating on the rear. Usually
the highest leg loads are a combination of loadings like a high speed bump at the same time as hard braking.
It occurs to me that looking at the picture, its failed in the obvious place (change in section) but because of the angle of failure and the fact that
the rear leg is intact, that braking force may have played a large part in its failure.
Obviously oval wishbones are very much stiffer in this load case than round section tubes.
If you use ERW tubing then you should give careful consideration to how you orientate the welded joint (ie put it on the neutral axis) so that you put
the least stress in that weak area.
Darren
|
PLEASE NOTE: This user is a trader who has not signed up for the LocostBuilders registration scheme. If this post is advertising a commercial product or service, please report it by clicking here.
|
blueshift
|
posted on 8/5/04 at 12:28 AM |
|
|
If bumps put up/down stress on the bones, and braking puts forward/back stress on them.. how should the ERW be aligned?
I might try and get some CDS or just get scared and rich enough to buy GTS bones 
|
|
NS Dev
|
posted on 8/5/04 at 08:57 AM |
|
|
I would use CDS anyway, made mine on my original car from 3/4" OD CDS hydraulic tubing.
|
|
NS Dev
|
posted on 8/5/04 at 11:07 AM |
|
|
Gosh, I have found somebody on the forum that I don't feel compelled to argue with!!
I agree once more Syd! Just as an aside, have a look at www.beardmorebros.co.uk, and take a look at the suspension design, chassis design etc on the
"New Project"
John Beardmore is one of the few people who designs things which I have great difficulty in criticising!! He should be at Curborough with it tomorrow
so I should be popping over for a look. Incidentally, Allan Staniforth has been looking at this car and has just done an article on the design etc of
it!
|
|
Bigfoot
|
posted on 8/5/04 at 04:22 PM |
|
|
From the beginning of the thread, I have been pushing the theory that it is just a badly designed wishbone, that failed ,mostly due to braking loads.
The other engineers on this forum with real experience in this field, appear to have a similar opinion. The problem lies more with the design than
the materials.
Cheers
Bigfoot.
|
|
britishtrident
|
posted on 8/5/04 at 05:19 PM |
|
|
quote: Originally posted by Syd Bridge
snip
snip
Given tubes of similar Moment of Inertia, both oval or round would be of similar suitability, with the round being preferable when buckling loads due
to compression are considered.
snip
Cheers,
Syd.
Since when did steel stock holders accept orders of tube in terms of "moment of inertia" ?
The tube is stocked by diameter or for oval tube major and minor dimensions.
An "oval" tube with minor dimension of 22 mm will have greater Second Moment of area than a 22 dia round tube.
It will be less efficient in terms of load carriying ability and stiffness to weight ratio but that is not the sole object. The use of oval tube of
say 22mm minor dimension is more acceptable when appearance is considered than 25 mm round tube which would look clumsy and out of place.
|
|