Chris Green
|
posted on 8/9/04 at 03:41 PM |
|
|
Sierra Rear Diff mounting Dimensions
Hello everyone,
Has anybody got the mounting dimensions for a sierra rear diff?
I've got this pic (Thanks to Craig Chaimberlain) can anyone provide any more info?
Thanks a lot!
Chris.
|
|
|
Chris Green
|
posted on 8/9/04 at 03:49 PM |
|
|
Sorry, Please ignore this. I've just realised that I have been sent a 3D model of it, and already have the dimensions!
Cheers,
Chris.
|
|
James
|
posted on 8/9/04 at 04:09 PM |
|
|
Is 3mm thick enough?
James
|
|
phelpsa
|
posted on 8/9/04 at 05:38 PM |
|
|
I was thinking that, I've made mine out of 6mm.
Adam
|
|
James
|
posted on 8/9/04 at 05:41 PM |
|
|
Ditto.
As is MK.
James
|
|
Chris_R
|
posted on 8/9/04 at 06:19 PM |
|
|
GTS use 5mm. There's a link to a PDF drawing of the rear of their kit on their site. It's at
http://www.cougarracing.fsnet.co.uk/dedion.pdf
Incidentally, if anyone has got a template I'd be interested.
Cheers,
Chris.
A bit of slapstick never hurt anyone.
http://www.chris.renney.dsl.pipex.com/
|
|
craig1410
|
posted on 8/9/04 at 06:30 PM |
|
|
James,
Mine are made from 3mm steel and they were originally supplied by MK Engineering as part of their de-dion kit. so I expect they are. I also have
additional mountings at the front of the diff which is also made from 3mm steel. The steel plates are fully welded to the chassis structure and the
structure as a whole seems very strong as the diff acts as a tie between all these mountings and adds to the strength. It might be different if the
diff was mounted on rubber mounts.
Suspension mounts are usually 3mm and are much smaller with less weld area than the diff mounts so I'd be more worried about them myself...
Cheers,
Craig.
|
|
andyharding
|
posted on 8/9/04 at 07:18 PM |
|
|
I've got a pair of brackets made out of 5mm plate by an engineering firm. As it happens I'm not going to need them. £10 + p&p if any
one wants them.
Are you a Mac user or a retard?
|
|
twinturbo
|
posted on 8/9/04 at 09:37 PM |
|
|
Got a pic Andy?
TT
|
|
andyharding
|
posted on 8/9/04 at 09:51 PM |
|
|
I'll sort one in the morning...
Are you a Mac user or a retard?
|
|
andyharding
|
posted on 9/9/04 at 08:28 PM |
|
|
Sorry for the delay, it's been a busy day.
The major squares on the graph paper are 1cm.
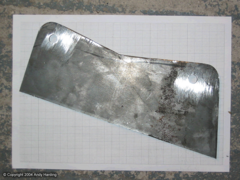 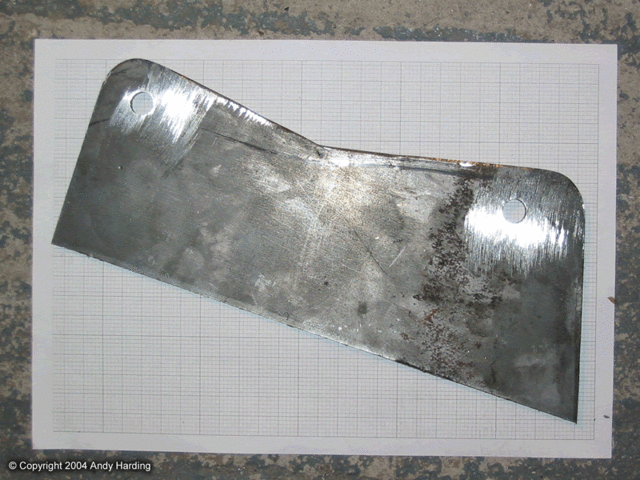 Diff Mount
Are you a Mac user or a retard?
|
|
Mix
|
posted on 10/9/04 at 07:09 AM |
|
|
I've used 3mm plate for my diff brackets as it's about the same size as Ford use. I can't see much point in using 6mm plate when you
are going to weld it to 1.2mm box section, surely it's just excess weight and more hassle to produce.
I will however be using the front and rear mountings on the diff in addition to the normal ones. the rear mount should add some rigidity to the IRS
'box' structure.
Mick
|
|
andyharding
|
posted on 10/9/04 at 07:44 AM |
|
|
I'm told MK originally used 3mm but switched to 5mm.
A kit car manufacturer wants to keep costs as low as possable so they wouldn't have done this if they did see good reason to.
Are you a Mac user or a retard?
|
|
craig1410
|
posted on 10/9/04 at 08:37 AM |
|
|
Mix,
Yes that was my thinking too and the supporting structure onto which the 3mm plates are welded is much more sturdy than the original MK design.
I'm not using the rearmost mount but I am using the other 6 mounting points.
At the end of the day it's an easy fix to add another chunk of 3mm plate to each side of the existing one if it proves insufficient but I doubt
that this will be required.
Cheers,
Craig.
|
|
James
|
posted on 10/9/04 at 09:03 AM |
|
|
Yeah, maybe you have a point. Perhaps mine's overkill.
I've only used the top and bottom mounts though. It's welded to a 25mmRHS and a 24*50*1.6 though so slightly stronger than Mick
suggests.
Maybe at this stage though I won't go cutting it out and replacing it with a 3mm piece!
James
|
|
craig1410
|
posted on 10/9/04 at 12:23 PM |
|
|
At the risk of being shot down in flames for over-simplifying the subject of structural analysis, here is some (probably flawed) rationale:
Mild steel has a typical tensile strength of the order of 400N/sqmm ( got that from some website)
A piece of 3mm mild steel, 200mm long has a cross sectional area of 600sqmm and hence can support 240000N of force, or roughly 24 Tons before it would
shear. 6mm steel would have twice this strength but is that really necessary?
Obviously this is a simple and probably flawed argument but even if you built in a "safety factor" of 10 then the 3mm steel plate could
still handle 2.4 Tons of mass hanging from it and there are two of them, one each side, holding my diff on plus another pair of plates attached to the
front of my diff.
My engine is a Rover V8 with about 270NM of torque at the flywheel and with an approximate 10:1 overall gear ratio in first gear this yields 2700NM at
the driveshafts. The diff mounts are something like 200mm apart, 100mm above and below the driveshaft centre and so the linear force felt at the
mounting bolts will be something like 2700/0.1 = 27000N. (lots of approximations here obviously)
So the force on the plates is of the order of 27,000N and the tensile strength of the pair of plates in 3mm steel is 480,000N. Plenty of headroom
there I think?
Okay, I'm standing by to receive a lesson in structural engineering from anyone who would care to point out the error's in my logic...
I expect that vibration, fatigue and welding quality and the effects of welding on the strength of the steel will be factors but regardless of this,
wouldn't the mounting bolts shear long before the 3mm plates failed? They are M12 size.
Cheers,
Craig.
|
|
Bob C
|
posted on 10/9/04 at 02:37 PM |
|
|
RE your 2700Nm on driveshafts - the wheels would slip! it's the ultimate torque limiting clutch. Assuming coeff friction to road is 1 you have
say 300kg on back axle - thats 3000N - at a radius of 30cm, ie 1000Nm.
500Nm on each side, rough estimate!
cheers
Bob
|
|
craig1410
|
posted on 10/9/04 at 03:12 PM |
|
|
Bob,
Yes that's a valid point!
In fact, going from those figures, I should be able to spin my wheels in any gear, including 5th!! That sounds like fun....
Anyone tried grafting a Formula 1 rear wing onto a Locost yet????
Cheers,
Craig.
|
|
mackie
|
posted on 10/9/04 at 03:35 PM |
|
|
Conrod said he could spin the wheels of his pretty standard pinto indy in 3rd
I recon our cars are going to be a bit of a handful craig 
|
|