JoelP
|
posted on 14/1/06 at 01:46 PM |
|
|
minor mig welder problem
hello all. The welders playing up.
The wire keeps sticking to the tip, which then causes the next attempt to push the swan neck out of the metal block in the handle. I think in the
beginning the rubber cover used to clamp it into the plastic handle, however its worn loose with age. I keep taking it apart and pushing it back
together, however i want to fix it perminantly cos it holds up progress. Question is, does this joint have to conduct electricity? i cant remember if
the current joins the wire in the large block in the handle or if the magic happens at the tip. The alternatives are simply glue it, or strip it and
solder it in perminant.
Also, the spring that runs inside the swan neck, is this needed? It has been melted onto the wire in the past as it all fell apart in my hand, still
useable but id rather have rid if its not needed.
As every your collective knowledge is appreciated
|
|
|
RazMan
|
posted on 14/1/06 at 02:28 PM |
|
|
I was advised by welduk.com to ditch the steel spiral inside the swan neck as it causes more trouble than it is worth.
Cheers,
Raz
When thinking outside the box doesn't work any more, it's time to build a new box
|
|
Peteff
|
posted on 14/1/06 at 04:28 PM |
|
|
My mate's had a plastic one in there and it melted, I had to blowlamp it to get the rest out. It's easier to get the wire through now. I
put a piece of airline round the swan neck up to the gas shroud, it looks and works like a new one now.
yours, Pete
I went into the RSPCA office the other day. It was so small you could hardly swing a cat in there.
|
|
Mark Allanson
|
posted on 14/1/06 at 06:06 PM |
|
|
Joel, how often do you change your tip? They do wear at an amazing rate. They should be replaced at least for every 5kgs of wire, more if using 0.6mm
wire
If you can keep you head, whilst all others around you are losing theirs, you are not fully aware of the situation
|
|
oliwb
|
posted on 14/1/06 at 07:31 PM |
|
|
Buy yourself a can of anti-spatter and spray it in the shroud and tip before you start welding and again periodicaly...it forms a kind of waxy
mambrane which will stop the weld adhering to it. It will also stop you from welding onto the tip and make your welds look nicer! It really does
work very well.....I'm runing mine with nothing in the swan neck at the moment though I'm about to extend my teflon liner up into it for
ali welding....The tip conducts the electricity to the filler wire but obviously it needs to get the current from somewhere - the swan neck so make
sure what ever you do doesn't insulate the two bits from each other.....best way of doing it is anything that involves bare metal touching bare
metal put it back together so that the end result is the same - eg no glue! Oli.
If your not living life on the edge you're taking up too much room!
|
|
JoelP
|
posted on 14/1/06 at 07:39 PM |
|
|
cheers chaps. Ive put it back together temporarily again, with a new tip (the old one was only about 2 weeks old, but my first one lasted 2 years!)
and it has started sticking immediately. So i conclude my settings are wrong. Would having the wire feed too low cause this? the rate seems fine from
the welds it does though. Its 0.8mm wire by the way, latterly being used on full power for tack welds.
As for the swan neck, im thinking soldering it in might be best.
|
|
JoelP
|
posted on 14/1/06 at 10:09 PM |
|
|
well, its gone from bad to worse! Just finished welding two 3x25mm flat bars together, and it melted the entire tip! Literally, had the full thing in
the sheath glowing red and drooping to one side.
Heres a picture of the results. It appears to have poor penentration at first, with far too much filler piled on top, but at the end its a melted
valley with far too little in it.
Any thoughts?
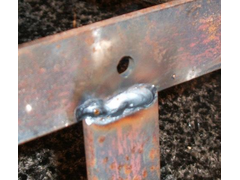  Rescued attachment weld.JPG
|
|
Mark Allanson
|
posted on 14/1/06 at 10:47 PM |
|
|
Sounds like the rollers are skidding and you have compensated by increasing the wire feed.
High initial build, followed by undercut and hollow weld and the wire balling back and fusing with the tip.
Joel, your first tip did not last for 2 years, it just didn't get changed for 2 years      
If you can keep you head, whilst all others around you are losing theirs, you are not fully aware of the situation
|
|
JoelP
|
posted on 14/1/06 at 11:29 PM |
|
|
quote: Originally posted by Mark Allanson
Joel, your first tip did not last for 2 years, it just didn't get changed for 2 years      
Its was about half the size it started as when i binned it, i kept filing it back to a point!
Cheers for the tips
|
|
lexi
|
posted on 15/1/06 at 12:45 AM |
|
|
Swan neck on SIP welders is held in by small allen screw that works loose as you clean shrouds and tips. I have to constantly tighten mine
Alex
|
|
Peteff
|
posted on 15/1/06 at 11:00 AM |
|
|
A friend of mine has fitted a euro conversion to his 150 amp welder and now uses a proper
Binzl torch. You can buy the torch complete with cable and liner for £35 from the same place and for less at places like
John Davies . These use real tips and shrouds and are ten times better than sip or clarke and
usually better price.
yours, Pete
I went into the RSPCA office the other day. It was so small you could hardly swing a cat in there.
|
|