jon_boy
|
posted on 10/2/06 at 11:31 AM |
|
|
Anti roll bars.
Im doing a project for uni and need some info. Immaking an adjustable stiffness balde type roll bar and im fine on the design but what material do
they use in tourings cars these days for them? Weve been told there is a specific material we should find. Cheers for any help, Jon
|
|
|
nitram38
|
posted on 10/2/06 at 11:44 AM |
|
|
Anti roll bars can be made of lots of different materials. The most common being steel. Some racecars use carbon fibre.
The thickness of the material is also important as some flex in the roll bar is required.
On my car in my avatar, I have used stainless steel. It is smaller in diameter than it's steel equivalent
[Edited on 10/2/06 by nitram38]
|
|
jon_boy
|
posted on 10/2/06 at 11:52 AM |
|
|
I thikn im meant to be aiming along the lines of high tensile aircraft grade but dont know what grade exactly. I think the blades are to be some sort
of titanium steel alloy. and i know they have to be machined in a way that isnt too normal ie spark erosion or something.. cheers for the info though!
|
|
Nick Skidmore
|
posted on 10/2/06 at 12:36 PM |
|
|
Any of the following:-
EN16T, EN19(EN equiv of T45), EN24T or 4130 (american grade).
Or any other grade of steel suitable for springs that isn't listed above.
|
NOTE:This user is registered as a LocostBuilders trader and may offer commercial services to other users
|
jon_boy
|
posted on 10/2/06 at 12:48 PM |
|
|
Top banana i'll try em out. Thank you !!
|
|
NS Dev
|
posted on 10/2/06 at 01:29 PM |
|
|
Nick, I know these are the "ideal" grades, particularly 4130, but I have successfully made bars from cold drawn mild steel tube with no
ill-effect. You have to watch that the linkage design can't push them beyond their elastic limits but that's not too tricky.
Main thing to watch out for is avoiding welds on them. You can get away with welds in some positions but generally they have a habit of breaking at
them!
Retro RWD is the way forward...........automotive fabrication, car restoration, sheetmetal work, engine conversion
retro car restoration and tuning
|
|
britishtrident
|
posted on 10/2/06 at 01:57 PM |
|
|
Its a leaf spring so look up the material for springs in "R Higgins" "Engineering Metalurgy--- medium carbon steel but with 1.9%
SI 0.85% to 1% Mn --- in addition 0.3% Cr and 0.25% Mo.
|
|
jon_boy
|
posted on 10/2/06 at 02:34 PM |
|
|
Basically its a theoretical design for a touring car so as light as possible but retaining stregth with no real budget. So anything is welcomed. I
have a plan for an in car adjustable system so will post the CAD files up when im done if anyone is interested. Jon
|
|
NS Dev
|
posted on 10/2/06 at 02:44 PM |
|
|
Ok, so don't use mild steel then!
Can it be of "any" design?
If so, remember that there's no reason not to use coil springs for anti-roll, no reason not to have a roll damper on the "antiroll
system" and adjustable antiroll spring preload.......................
just to give you some more ideas/confusion!
Retro RWD is the way forward...........automotive fabrication, car restoration, sheetmetal work, engine conversion
retro car restoration and tuning
|
|
JB
|
posted on 10/2/06 at 05:50 PM |
|
|
ARB`s
The welding point is very relevant.
I use Loctite 638 high strength retainer to bond the arms onto the ends of my straight bars.
John
|
|
NS Dev
|
posted on 10/2/06 at 07:29 PM |
|
|
Call me stupid but I hadn't thought of that one John! I was scratching my head for ages when I did the rear bar for the grasser, as to how to
attach the blades without access to a milling machine............
in the end I just made the blades as part of the bar, just "warm" bent it at each end to form the blades.
Retro RWD is the way forward...........automotive fabrication, car restoration, sheetmetal work, engine conversion
retro car restoration and tuning
|
|
Sirius
|
posted on 10/2/06 at 07:45 PM |
|
|
Very useful post
As a slight off-topic, I have read that its best to have as few bends as possible in an ARB, however if you must have a bend because its fitted to a
road car for example - whats the best way of getting the bend into it?
Heating and a bar bender? Would the material alter the bending method?
Cheers 
|
|
JB
|
posted on 10/2/06 at 07:53 PM |
|
|
When I make my ends to put onto the bar I actually taper the outside from down to very thin on bar end. This hopefully will reduce the stress raiser
where the Loctited end goes onto the bar.
I make the tube that I Loctite about 120mm long. You could work out the maths but I just use judgement.
John
|
|
NS Dev
|
posted on 10/2/06 at 08:48 PM |
|
|
quote: Originally posted by Sirius
Very useful post
As a slight off-topic, I have read that its best to have as few bends as possible in an ARB, however if you must have a bend because its fitted to a
road car for example - whats the best way of getting the bend into it?
Heating and a bar bender? Would the material alter the bending method?
Cheers
The way I did it was nothing but a bodge really, but it worked extremely well so I have done it that way again since!
Reason I did it was cos I didn't have the right former for the 11/16" OD cds tube that I used!
I just heated it to dull red with a blowlamp then bent it in the vice a little bit at a time until I got the required angles in a smooth curve.
It's very thick wall tube (just under 4mm wall) so it didn't kink.
It was a late addition to the grasser after a few events hence the wrong colour paint, the suspension is on full droop hence the odd anges (it has
12" of wheel travel!) and the car is in bits for an engine check over:
see below!:
 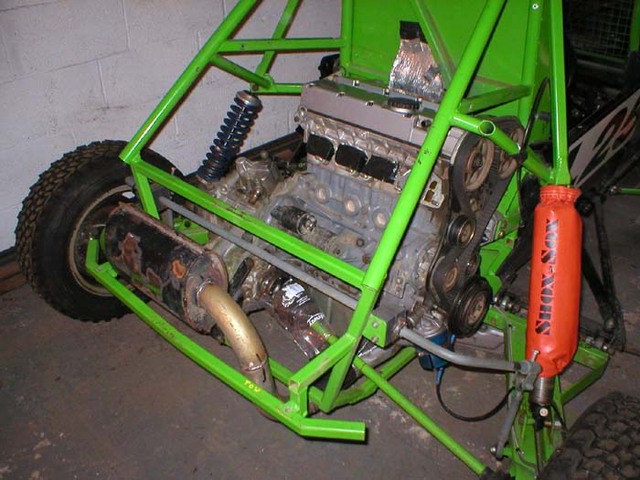 Grasser rebuild, race in 1 wk!
[Edited on 10/2/06 by NS Dev]
Retro RWD is the way forward...........automotive fabrication, car restoration, sheetmetal work, engine conversion
retro car restoration and tuning
|
|