gregf27
|
posted on 4/6/06 at 07:55 PM |
|
|
F27 Owners urgent safety warning!!!
Went for a run in my plan built F27 on Tuesday , and as I was approaching a junction, I heard a loud "POP" and the off side front wheel
canted over and locked up.!!
On checking what had happened , the weld around the nut on the lower wishbone had snapped!!!
This has happened to at least one other F27 owner ( Bruce Jackson ) that I am aware of ,
I am sure that this could happen to anyone else with this type of designed lower wishbone.
PLEASE can the F27 owners / builders check their wishbones , and carry out the strengthening suggestions that I have just completed ( photos in my
archive )
Luckily I was travelling slowly and there were no injuries , Damage wise , I have had to replace the steering rack ,as it had pulled one of the racks
out by 20mm!! 
Luckily I had a spare rack in my garage!!
If this post helps to avoid even a single accident or injury then I will feel good!!
I'll try to post a pic or two now!
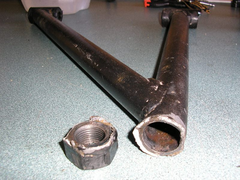 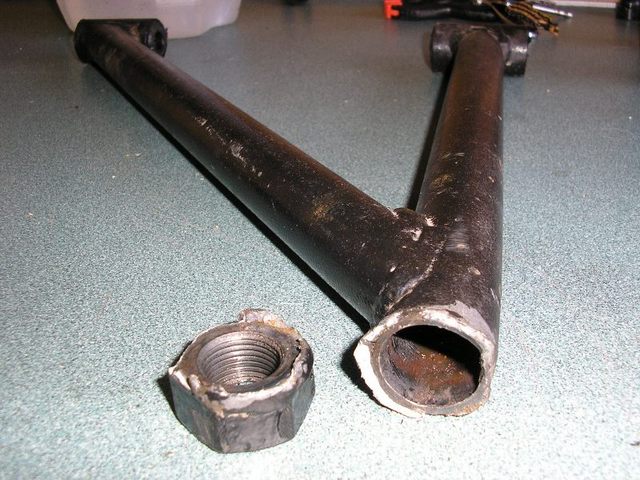 F27 lower wishbone snapped
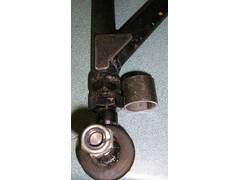 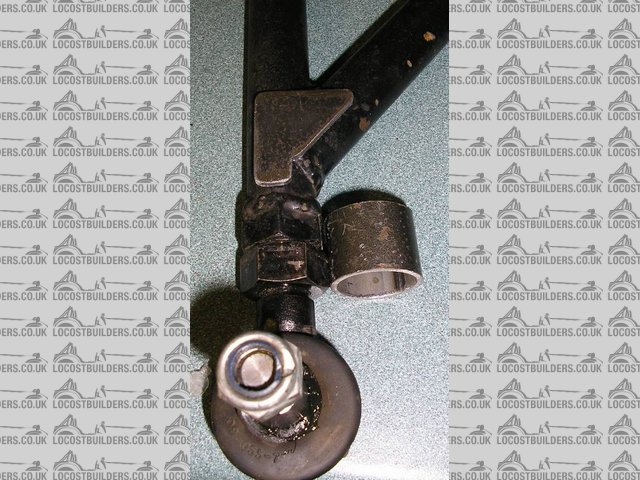 F27 wishbone strengthening par
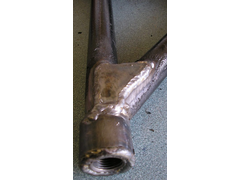 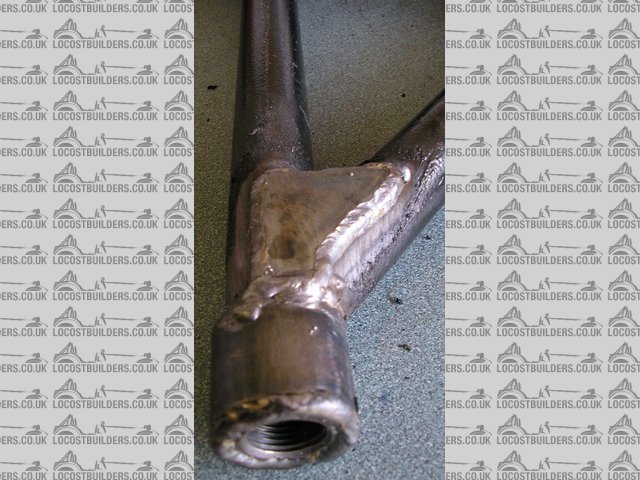 F27 wishbone underneath
|
|
|
ChrisGamlin
|
posted on 4/6/06 at 08:05 PM |
|
|
Jesus thats scary, I cant believe they just welded on a bolt like that!
|
|
omega 24 v6
|
posted on 4/6/06 at 08:15 PM |
|
|
Looks like a severe lack of penetration. I wonder what the rest of the welding is like   
|
|
Confused but excited.
|
posted on 4/6/06 at 08:25 PM |
|
|
Jeez! How scary is that?
Just 'cos you bought it, obviously don't mean it's safe.
Why in hell would anyone do something so stupid!
Tell them about the bent treacle edges!
|
|
t.j.
|
posted on 4/6/06 at 08:31 PM |
|
|
Who fabricated that???
I would make an insert and drill two holes which would give extra strenght.
Hopefully, the other drivers check-up their arms.
|
|
JoelP
|
posted on 4/6/06 at 08:31 PM |
|
|
never heard of a threaded insert i guess! thats some bleak stuff...
|
|
aerobrick
|
posted on 4/6/06 at 08:32 PM |
|
|
Jesus I am just about to assemble my f27 suspension its all new in the box looking at that failure i will have a really good look
May even post a photo on here showing what the bought new from YKC before don sold the whole shebang Last year.
I will be modding mine I simply do not like the way its designed.
|
|
Jon Ison
|
posted on 4/6/06 at 08:32 PM |
|
|
I must say the weld looks a bit dodgy but the idea is even more dodgy, that's a very highly stressed area of any car.........
 
|
|
DIY Si
|
posted on 4/6/06 at 08:42 PM |
|
|
Weld looks to have barely attched the nut to the bone tube. There is surely a better way to make these things? Just out of curiousity, how do the
inserts weld in? I've never seen one up close before.
|
|
MikeRJ
|
posted on 4/6/06 at 08:53 PM |
|
|
quote: Originally posted by gregf27
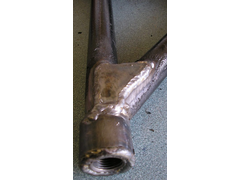 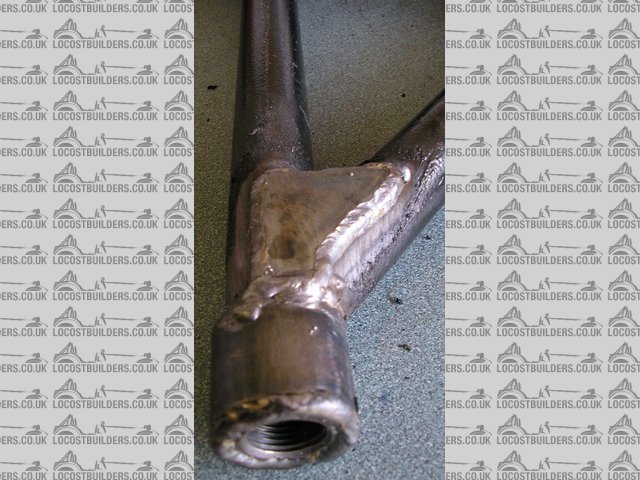 F27 wishbone underneath
Your going to have to remove a lot of that outer weld to get a flat surface for the lock nut to seat against. I'd be tempted to drill a couple
of holes though the side of the tube and put some plug welds in for extra security. A proper threaded insert would be better again.
|
|
ChrisGamlin
|
posted on 4/6/06 at 08:55 PM |
|
|
A much better way to do it would be to make up a long threaded insert that would support the entire length of the ball joint, then slide that inside
the tube and weld it in. You'd probably puddle weld it in as well so its welded at both ends of the tube.
|
|
DIY Si
|
posted on 4/6/06 at 09:13 PM |
|
|
So, do you buy the inserts or make them? Never treid to find any before. Would you normally put plug welds down the length of them or not?
|
|
JoelP
|
posted on 4/6/06 at 09:19 PM |
|
|
you can make or buy them, id buy them myself as i dont have a lathe to make them on. Nick skidmore has in the past made them, i hope to buy a
selection and some roses off him 
|
|
Deckman001
|
posted on 4/6/06 at 09:37 PM |
|
|
Isn't that the way Gts offer for wishbone design(Adjustable Insert) Sounds like he is ahead of the game
Jason
|
|
nitram38
|
posted on 4/6/06 at 09:56 PM |
|
|
For my bones I used 30mm long 20mm dia 1/2" UNF bushes.
Instead of them being welded onto the end of tube, my tubes meet either side of the bush. This means that the surface area of the weld is the full
length of the bush. Also a small piece of 10mm tube is triangulated between the 2 joining tubes.
[img][/img]
|
|
Liam
|
posted on 4/6/06 at 10:53 PM |
|
|
Hello...
Forgive me for being critical, but I dont think that strengthening is going to do a thing! The weak point is still exactly the same as it was before
- where a nut is welded onto the end of a tube. That plate may help the wishbone as a whole but wont help the weld that failed at all. And the
sleeve over the two nuts also wont help the weak weld - the inner weld of that sleeve is simply on top of the weld that failed. No part of that
strengthening has actually strengthened that original weld imho. I think the only way to do it is with threaded inserts like everyone else has
suggested.
Liam
[Edited on 4/6/06 by Liam]
|
|
JB
|
posted on 5/6/06 at 04:46 AM |
|
|
SVA, Design etc
You will fail an SVA for a radius that is too small but something like that, which is just shocking, doesnt get picked up.
Poor penetration is not the real problem it is poor design.
Welds should never be loaded in tension (pull) but in shear. You should get as much weld surface area as possible.
Which is why you should have a threaded insert, that slots into the tube. The end of the tube is slash cut (not square). The slash cut gives more weld
area and puts the weld in shear.
A couple of rosette welds are a good idea. Rosette welds are where you put a hole in the outer tube (6mm) and weld through into the inner tube, a bit
like a big spot weld.
John
|
|
britishtrident
|
posted on 5/6/06 at 06:52 AM |
|
|
I don't think the mod hs fully addressed the reall cause of the failure
Personally I would have used a long threaded insert bronze welled/brazed in or used thick wall tube and tapped the thread on to the tube as per book
Locost top wishbone..
[Edited on 5/6/06 by britishtrident]
|
|
Hellfire
|
posted on 5/6/06 at 08:13 AM |
|
|
I'd say poor design too...
How the hell a nut welded onto the end of a pipe is supposed to support anything like a suspension component is beyond me.
Either a insert brazed in or even pinned is better than the option used. A severe redesign is vital to prevent this happening in the future. As a
critical part you would expect nothing less really...
|
|
nitram38
|
posted on 5/6/06 at 09:39 AM |
|
|
Not a very good picture, but it shows how I cut half of the tube away and welded the bush in. On my outboard joints, both tubes meet each side of the
bush, but with enough gap to weld all 3 componants. Please ignore the nut cover/lock wire, it is for my up coming sva.
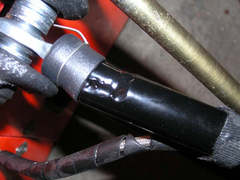 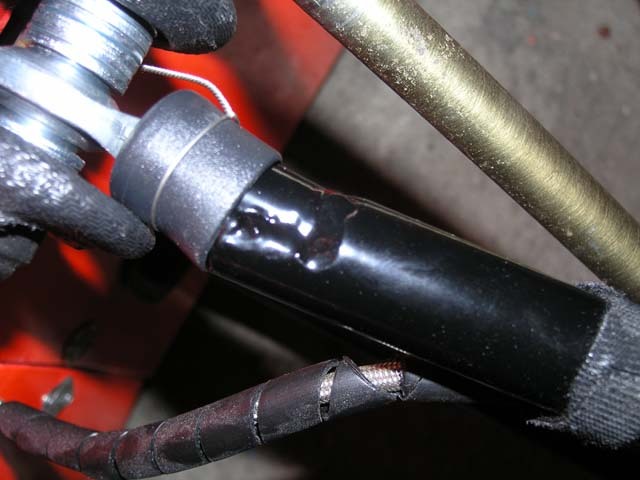 Description
[Edited on 5/6/2006 by nitram38]
|
|
David Jenkins
|
posted on 5/6/06 at 09:44 AM |
|
|
quote: Originally posted by Hellfire
I'd say poor design too...
How the hell a nut welded onto the end of a pipe is supposed to support anything like a suspension component is beyond me.
Either a insert brazed in or even pinned is better than the option used. A severe redesign is vital to prevent this happening in the future. As a
critical part you would expect nothing less really...
I was surprised to see the same technique used by a so-called top hot-rod builder in a programme on Sky - they were making the rear swinging arms by
welding nuts onto the end of steel tube. A few tack welds, fit the rose joints, try them for size, then strip down and fully weld. If I was paying
over $50000 for a car I'd expect better engineering than that!
David
P.S. It wasn't American Hotrod - it was some other show.
|
|
DarrenW
|
posted on 5/6/06 at 10:00 AM |
|
|
Defo bad design. Nitram has the better idea of sandwiching the 2 wishbone tubes either side of a threaded insert and fully welding.
My lower 'bone takes the lower ball joint that bolts onto a plate. Not as adjustable but defo stronger.
Its amazing what some people offer for sale!
|
|
JB
|
posted on 5/6/06 at 10:14 AM |
|
|
Quote"I was surprised to see the same technique used by a so-called top hot-rod builder in a programme on Sky"
Doesnt surprise me. Unfortunately a lot of hot rodders are also ignorant of good design. They can build big engines, craft nice looking pieces of
metal and have great paint jobs but fundamental good design is often lacking.
John
|
|
britishtrident
|
posted on 5/6/06 at 11:23 AM |
|
|
Some 20 years ago I remember looking at a Rover V8 powerer T bucket Hot rod. To get the steering coloumn to clear the engine the bulider had used a
Viva steering rack mounted off centre by about 200mm from the vehicle centreline and one track rod was extended in length to accomodate this. What
really irked me was the driver and I presume builder of the Hot Rod was acting as a RAC MSA assisant scrutineer.
|
|
pewe
|
posted on 5/6/06 at 11:26 AM |
|
|
Greg. that's a bug*er I've not long had mine done by my local pro. welder. Must say he wasn't over-keen to do it that way though -
same as JB's comments about shear rather than tension. Suppose I'll have to find some inserts - one step forward and two back as usual!
Cheers for posting it - I thought Bruce's was a one-off, Pewe.
|
|